3D Printing Titanium Services
3D printing solutions provided by Wstitanium include: DMLS, EBM. Manufacture fully functional titanium prototypes and custom titanium parts in 7 days or less for final parts for end-use applications.
- Production-Grade Material Prototyping
- Arbitrary Complex Geometries
- Tight Tolerances +/- 0.002”
- Reduce Steps In Assembly
- Functional End-Use Parts
Wstitanium Workshop
Our Powerful Facilities
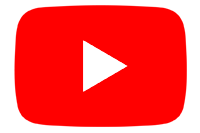
3D Printing Services for Titanium Parts
Titanium is a difficult metal to machine, especially when it comes to CNC machining. For one thing, titanium has a low thermal conductivity. This means that when a CNC machine, for example, performs milling, the heat generated is stored in the tool. This can cause the tool to wear quickly. In addition, since machining involves cutting and removing material, the process can result in a lot of material waste. As a result, many companies are looking for better alternative solutions to manufacture titanium parts. Metal 3D printing of titanium is proving to be a viable alternative. The most commonly used titanium grade is the alloy Ti6Al4V (Ti64). In addition to Ti64, pure titanium can also be used for 3D printing.
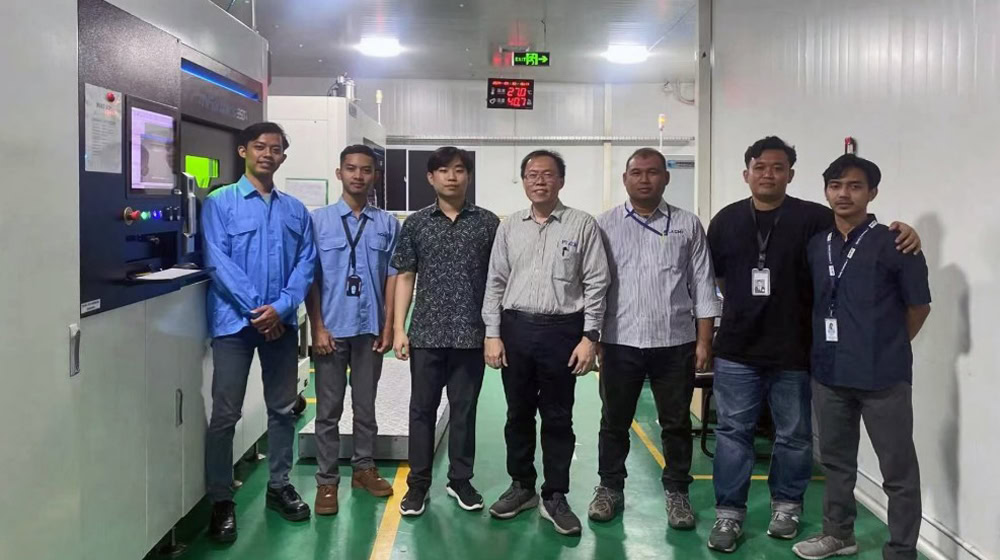
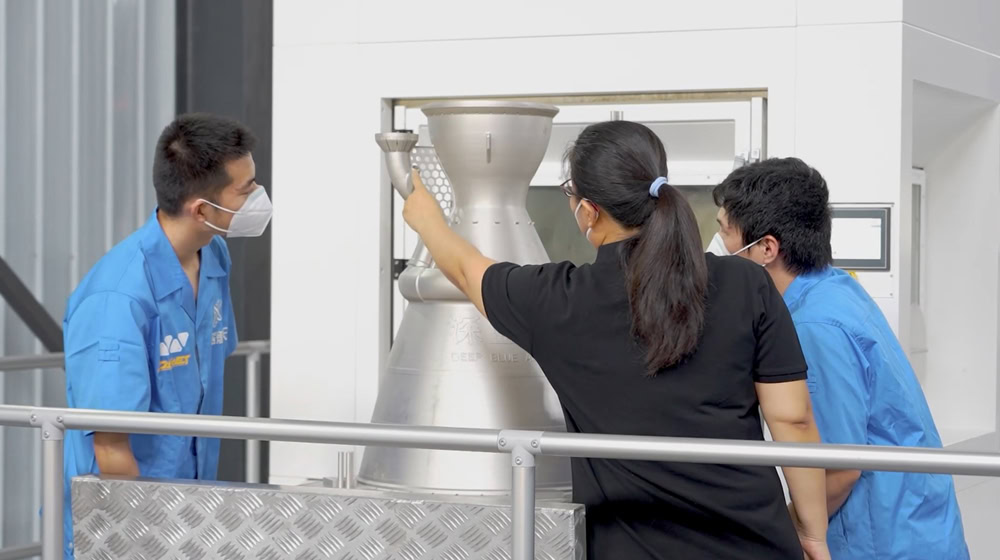
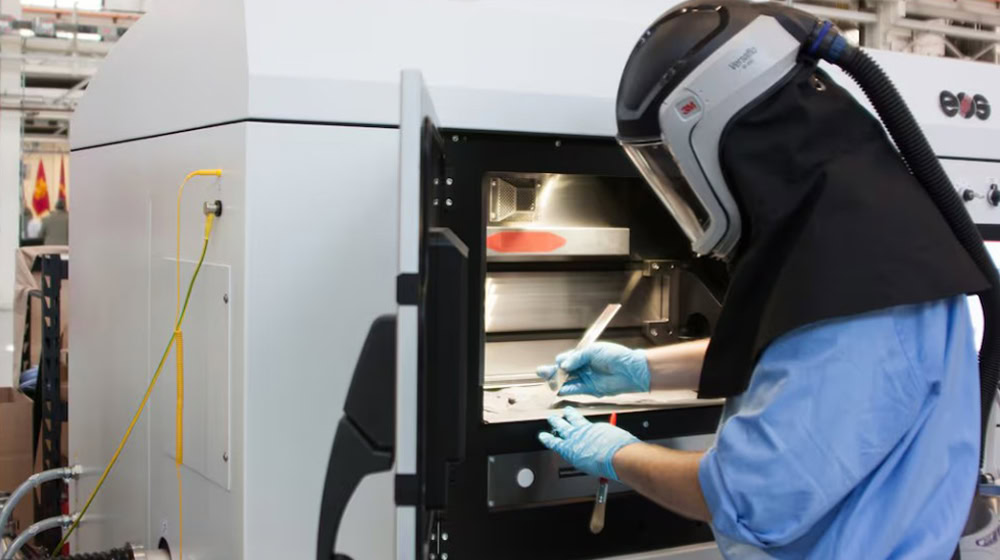
Wstitanium 3D Printing Workshop
Advantages of 3D Printing Titanium
3D printed titanium can be manufactured economically in small and medium batches. It is a more cost-effective option compared to methods such as CNC milling, turning or casting, as the cost does not depend on the complexity of the part. All that is needed to successfully manufacture titanium products is a 3D printer and metal powder, rather than relying on expensive tools or complex specialized solutions.
Reduced Waste of Material
Compared to traditional subtractive manufacturing processes, such as CNC machining, 3D printing is an additive manufacturing technology that does not generate a lot of material waste. During the manufacturing process, the remaining titanium powder can be used for the next print. In addition, 3D printing titanium can produce parts very close to the final desired shape, reducing the need for extensive post-processing and further reducing waste.
Design Optimization
3D printing is able to create parts with complex, lightweight structures that are difficult or impossible to manufacture with traditional methods. This means using less material while maintaining strength and functionality. One of the ways engineers achieve design optimization is through topology optimization in CAD software, which consolidates multiple parts into a single printed part, which can reduce assembly time, labor costs and potential failure points.
No Tooling or Setup Costs
For either casting or CNC machining titanium parts, custom tooling such as molds, fixtures, etc. is required. 3D printing eliminates the need for additional tooling because the parts are printed directly from the digital file. Changes to part design can be implemented quickly without the need for new tooling, reducing the costs associated with design modifications.
Shorter Leading Time
Wstitanium uses an in-house metal 3D printer, and the delivery of a single part may take only 1 day, while CNC machining and casting may take longer (as mentioned above, they require the help of tools or fixtures). 3D printing services have shorter manufacturing times and you can order parts on demand without the need for inventory reserves. This greatly reduces the risk of capital.
Customization and flexibility
3D printing allows custom parts to be made without reassembly, making it easier and more cost-effective to produce small batches or customized products, further reducing operating costs. For example, patient-specific surgical tools.
Energy efficiency
3D printing titanium services, such as electron beam melting (EBM) or selective laser melting (SLM), are more energy-efficient than CNC machining, especially when considering the reduced need for post-processing and material recycling.
Wstitanium In-house 3D Printing Technology
Since 2019, Wstitanium has spent more than $2 million to invest in metal 3D printing technologies, such as DMLM, DMLS, LPBF, and LMF. Among them, laser powder bed fusion (LPBF) is the most common.
Direct Metal Laser Sintering (DMLS) is similar to Laser Sintering Technology (SLS), but instead of using polyamide, fine titanium powder is used to build the model layer by layer. A thin bed of titanium powder is laid down in the 3D printer. This layer is then sintered and solidified by a very powerful laser and will become the bottom layer of the part. The laser beam moves over a box filled with powder. After each layer, a new layer of powder is applied. The process is then repeated. Remove your part from the 3D printer and clean off any loose, unsintered powder. In most cases, there will be 3D printing support structures made of titanium on and around your part. These supports must be removed manually using very powerful circular saws and other tools. Once the supports are removed, manual polishing is required to remove traces of the supports. Post-finishing steps may then be required, such as polishing the entire part.
- Maximum titanium part size: 250 x 250 x 320 mm
- Minimum titanium part size: 5 mm x 5 mm x 5 mm
- Default Layer Height: 0.04 mm
- Optional Layer Heights: 0.05mm
- MOQ=1
- Tolerance:±0.02mm
- Surface Roughness: 150-400 Ra
- Cost: Depends Mainly on Weight
EBM (Electron Beam Melting) refers to the electron beam being applied to a layer of titanium powder, melting it and fusing it with the previous layer. EBM utilizes a high-energy electron beam under vacuum to melt titanium powder. The beam scans over a bed of titanium powder, melting and solidifying the material layer by layer according to a digital design. EBM is considered more precise than DMLS and is suitable for making smaller, complex titanium parts. EBM is particularly effective in controlling the reactive properties of titanium because the vacuum environment prevents oxidation, a common problem when titanium is heated in air. The electron beam can also dynamically adjust the focus and power, allowing for precise control of the melting process, which is critical to maintaining the performance and structural integrity of titanium parts.
- Maximum titanium part size: 210 x 210 x 400 mm
- Minimum titanium part size: 5 mm x 5 mm x 5 mm
- Elastic modulus: 113.8 GPa
- UTS Mpa: 1033
- MOQ=1
- YS 0,2 Mpa : 973
- Elongation: 15,6 %
- Tolerance:±0.02mm
The EBM process, on the other hand, is carried out under vacuum and at high temperatures. This results in minimal residual stress in 3D printed parts, which also means that these 3D printed titanium parts do not require subsequent heat treatment.
Titanium Alloy Grades for 3D Printing
The most commonly used titanium grade for 3D printing is the alloy Ti6Al4V (Ti64). In addition to Ti64, pure titanium can also be used for 3D printing. As 3D printing technology develops, material manufacturers create a variety of titanium powders suitable for 3D printing. These metal powders are carefully designed with uniform particle size and shape, which improves fluidity and packing density on the print bed. This enhancement enables smoother and more detailed printing and enhances mechanical properties by reducing inclusions and porosity. Most titanium 3D printing uses titanium alloys (metal materials containing alloys of titanium with other elements) rather than pure titanium. The type of titanium alloy used depends on the specific 3D printing application. Some common varieties are shown in the table below.
Alloy | Grade | Description | Applications |
Ti-6Al-4V | 5 | The most common and important titanium alloy for 3D printing, with excellent strength-to-weight, corrosion resistance, and biocompatibility | Aerospace components, automotive components, surgical instruments, medical implants |
Ti-6Al-4V-ELI | 23 | This purer titanium alloy has an “extra-low interstitial,” making it slightly weaker than Grade 5 but better for biomedical applications | Surgical instruments, medical implants |
Ti-6Al-2Sn-4Zr-2Mo | A near-alpha titanium alloy with high strength and excellent corrosion resistance | Aerospace components, aviation components, marine components | |
Ti-5Al-5V-5Mo-3Cr | A beta titanium alloy with high strength and toughness that shows promise in 3D printing due to its poor machinability | Industrial components |
Titanium grade 5 6Al-4V is the most commonly used titanium alloy in additive manufacturing and is ideal for prototypes and functional parts in the aerospace, automotive and military sectors. It is also an excellent material for manufacturing parts with complex geometries and precision, as well as production tools. Titanium grade 23 6Al-4V is a biocompatible alloy that is often used in medical implants and prosthetics. Beta 21S grade titanium has higher strength than traditional titanium alloys such as Ti-6Al-4V, and also has better oxidation and creep resistance than traditional titanium alloys such as Ti-15V-3Cr. Of all titanium alloys, 21 grade titanium has the lowest hydrogen absorption efficiency. It is ideal for orthopedic implants and aerospace engine applications. Beta titanium is widely used in dental corrections. Cp-Ti (pure titanium) grades 1 and 2 are widely used in the medical field due to their biocompatibility with the human body. TA15 is a near-alpha titanium alloy with aluminum and zirconium additives. Parts made from TA15 have high specific strength, high load-bearing capacity and temperature resistance, so they can be used for heavy parts in aircraft and engine manufacturing.
Surface Treatment of 3D Printed Titanium Parts
Wstitanium offers titanium components with specialized surface finishes. Options such as strength, rust resistance, and metal conductivity can be added to titanium parts during post-processing. Surface treatments provided by Wstitanium’s titanium 3D printing services include shot peening, electrochemical polishing and CNC machining, heat treatment, and more.
Sandblasting
Sandblasting can remove defects, pits, rust and other contaminants from the surface of parts. Sandblasting is often used to prepare parts for coating. Different sandblasting methods include micro-sandblasting, brush blasting, bead blasting, etc. Sandblasting uses abrasives such as steel grit, silicon carbide, pumice, etc.
Shot Peening
Shot Peening can enhance the strength of a part and reduce its stress distribution. During the shot peening process, the part is subjected to multiple shots, which leave deformations on the surface of the part. The process adds a compressive stress layer.
Optical Polishing
Optical polishing is cost-effective and provides a bright surface effect. Optical polishing creates a micro-finish or super-finish on the surface of the part in preparation for further processing. Optical polishing processes are best suited for projects with low-volume, non-tolerance dependent geometries.
Electrochemical Polishing
Electrochemical polishing produces a mirror-like finish on metal parts and can also be used to prepare a part for further finishing. In this process, the part is placed in an electrolytic solution with a copper or lead cathode. An electric current flows through the solution, smoothing the surface of the part.
Electroplating
Electroplating adds a metal layer to the outside of a part, increasing its strength and durability. Electroplating dissolves the metal in an electrolytic solution and transfers it to the surface of the part. Some of the most common metals used in the electroplating process are copper and zinc.
CNC Finishing/Machining
CNC machining adds wear resistance, metal conductivity, strength, rust resistance, and more. CNC finishing can improve the appearance of the part and prepare it for final coating. Finishing may involve powder coating, sandblasting, passivation, and anodizing.
Heat Treatment
Heat treatment improves titanium’s mechanical properties, such as strength and toughness. This is a critical step for parts that are subject to high stresses.
Titanium TiAl4V Heat Treated | Value |
---|---|
Yield Strength Rp 0.2% | 950-1050 MPa |
Ultimate Tensile Strength Rm | 1000-1150 MPa |
Elongation at Break | 9-15% |
Young’s Modulus | 105-125 GPa |
Relative Density | 99.5% |
Hot Isostatic Pressing (HIP)
HIP eliminates internal porosity in titanium parts, making them denser and stronger. During this process, the titanium alloy is heated to 1000⁰C for 60 minutes in an argon atmosphere and then slowly cooled.
Titanium TiAl4V HIP | Value |
---|---|
Yield Strength Rp 0.2 % | 870-950 MPa |
Ultimate Tensile Strength Rm | 950-1050 MPa |
Elongation at Break | 13-16 % |
Young’s Modulus | 105-125 GPA |
Relative Density | 99.5% |
3D Printing Titanium Parts Application
3D printed titanium parts are a major focus in the manufacturing industry. Titanium 3D printing has changed the rules of the game in multiple fields, aiming to provide lightweight and strong products with innovative (often customized part) designs. The most important areas of application of 3D printed parts are: aerospace, medical, automotive, bicycle/racing, chemical, marine, etc.
Titanium’s non-toxicity, high strength, and corrosion resistance make it an attractive material for orthopedic and dental implants. As more and more medical manufacturers allow 3D printing services in their manufacturing capabilities, the number of titanium-based printed surgical implants approved by the US FDA continues to grow. When combined with 3D printing, medical device manufacturers can manufacture implants with complex porous structures. Notably, these structures mimic the structure of human bones, so bone cells recognize them as scaffolds for growth. In the medical industry, 3D printed titanium implants have been successful in spine, hip, knee, and limb applications because of titanium’s inherent biocompatibility and good mechanical properties. In addition, the ability to 3D print customized porous structures (thus achieving bone integration) and mass customization capabilities better achieve therapeutic effects for patients.
In 2023, Wstitanium’s 3D printed parts for wrist and ankle replacements for patients treated at the University Hospital of North Midlands in the UK received high praise from medical and patients.
Titanium’s strength-to-weight ratio enables the production of complex components that are lighter and more durable than those made from traditional materials, making aircraft not only more fuel-efficient but also able to withstand the extreme stresses of flight. In the aerospace industry, some titanium-based 3D-printed manufactured parts are currently used in commercial and military applications, and many other prototypes are in the process of obtaining certification from the Federal Aviation Administration. 3D-printed titanium parts are highly regarded for their low “buy to fly” ratio, an aerospace term that refers to the correlation between the weight of the initial material and the weight of the printed part. 3D-printed titanium parts help reduce the weight of highly loaded structures, making them ideal for jet engines, gas turbines and many airframe components.
For example, Liebherr reduced the weight of the bracket by 29% and increased its stiffness. Aerospace supplier Liebherr-Aerospace & Transportation SAS will begin serial production of 3D-printed titanium nose landing gear brackets for the Airbus A350 XWB in 2023. These brackets will be the first Airbus parts to be produced using 3D-printed titanium.
The automotive industry has not been as fast to adopt titanium 3D printing compared to the aerospace and medical industries. Despite offering the same benefits, the consumer automotive market is very cost-conscious, which limits the use of this expensive material in most vehicles. 3D printed titanium parts facilitate the development of custom high-performance cars. Manufacturers can create lightweight but strong titanium parts such as gears and brackets, which helps reduce the overall weight of the vehicle and improve performance. This application is crucial in the electric vehicle sector, where efficiency and battery range can be significantly improved by reducing vehicle weight. Currently, titanium 3D printed parts are widely used in racing and luxury cars, where weight and performance are important factors.
In automotive, one of the most prominent examples of titanium 3D printing is the brake caliper developed by Bugatti for its Bugatti Chiron supercar. The brake caliper, an important part of the braking system, measures 41 x 21 x 13.6 cm and was 3D printed in 45 hours using DSLM technology. The finished part is said to be about 40% lighter than the machined aluminum alternative. In 2022, Wstitanium designed a titanium exhaust pipe for the Formula One car of the Oxford Brookes student team in the UK, achieving a 50% weight reduction.
3D printed titanium is almost commonplace in today’s high-performance bikes, where every ounce of weight and high strength is critical. A lightweight all-titanium frame, which accounts for crucial seconds in race times and enables new design geometries, is 400 grams lighter than the previous aluminum 7075 version. Titanium is also used to make cranks, brake levers, stems, derailleur hangers, and even full frames, proving to be as strong as aluminum and as light as carbon fiber without facing the sustainability challenges of carbon fiber. 3D printed titanium makes it possible to customize the bike to the rider’s preferences, and the frame does not require any paint or coating.
Wstitanium will increase its titanium 3D printing efforts in 2024, planning to use 3D printing technology to manufacture titanium bicycle frames and components, with an annual output of more than 2,000 pieces. Titanium components will be used on a variety of bicycle models, aiming to provide customers with titanium bicycle products with higher strength, lighter weight, and more durability.
3D Printing Titanium Parts Design Optimization
Titanium is by far the strongest 3D printing material from Wstitanium. You’ll notice this too when you design 3D models for this material. To get the better titanium 3D prints you’re looking for, here are some simple tips you should keep in mind:
Wall Thickness: The minimum thickness of the “wall” can be as low as 0.4 mm! For most materials, this value is typically 1 to 3 mm. Wstitanium recommends sticking to a minimum wall thickness of at least 1 mm for titanium parts.
Detail Size: With a DMLS printer, you can print very fine details. The distance between the model wall and the detail surface can be as small as 0.25 mm!
Precision: Due to the thermal expansion and contraction of titanium metal, 3D prints may be slightly larger or smaller than your original design. However, DMLS is by far the most dimensionally accurate metal 3D printing process. For titanium alloys, the accuracy is typically better than 2%.
Geometry: Right angles and straight lines tend to look less attractive than organic or free-form shapes. Angles less than 35° tend to result in poor surface quality. Steep angles over 35° tend to produce finer, smoother, and better-looking surfaces. DMLS is the best option for making mesh-shaped parts.
3D Printed Titanium Parts Gallery
Wstitanium manufactures 3D printed titanium parts for a variety of fields, including bicycles, aerospace, medical, and more.Titanium (TiAl 6 V 4 ) is a very strong, lightweight, corrosion-resistant metal material. 3D printing refers to printing titanium powder together with a laser to sinter it to create parts that are as good as machined models. 3D printed titanium (unpolished) does not look like traditional shiny milled titanium. Instead, it has a matte gray finish that is slightly rougher and less defined, or a slightly reflective satin finish.