CNC Tapping Services
CNC tapped titanium parts undergo rigorous quality inspections to ensure thread integrity and dimensional accuracy. Wstitanium’s quality control is implemented throughout the manufacturing process, immediately identifying and addressing any deviations from the standard, ensuring that each titanium part meets the high quality standards of ISO2768-Fine.
- ISO 9001:2015, ISO 13485 Certified.
- Tolerances Up to ± 0.005mm
- 100% Quality Inspection Report
- Pay After Delivery
WSTITANIUM Factory
Our Powerful Facilities
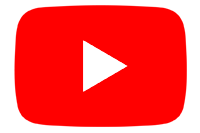
CNC Tapping - Creating Internal Threads for Titanium Parts
Wstitanium recognizes that every CNC project has unique requirements and provides custom CNC tapping services. The technical team works directly with you to understand your specific needs. Whether it is a unique thread type or a challenging titanium material, expertise and technology are designed to provide solutions that meet precise specifications. For precision tapping CNC projects, Wstitanium is your trusted partner. Whether you need a small batch of custom parts or a large-scale production run, our expertise in CNC tapping will ensure your project is a success. Allows creation of various thread types such as: metric, UNF, UNC, and specialized threads like NPT and acme.
What is CNC Tapping?
Have you ever questioned how threads are created on metal parts or workpieces? CNC tapping is the process that makes it happen. CNC tapping is the process of creating internal threads within a hole in a part to accommodate a bolt or screw. A tool, usually a tap, is used to cut threads within a pre-drilled hole. Tapping is essential to creating secure connections between various components. This technology is part of CNC machining so it can consistently create precise threads.
How does CNC tapping work?
CNC tapping uses a tool called a tap. The tool rotates in a hole in the material to cut out threads. The tap has a cutting edge that removes excess material to form threads that are designed to match the screw or bolt that will be used. Tapping can be done either with a manual tap or automatically with a CNC machine, depending on the accuracy and repeatability required. CNC tapping generally has higher precision and repeatability. Tapping is essential in applications that require threaded holes for assembly, such as automotive, aerospace, marine, mechanical equipment, etc. Let’s take a closer look at how tapping works.
Cleaning the surface of the part
Before tapping, proper preparation of the workpiece surface is a must. For example, cleaning and, if necessary, applying lubricants or cutting fluids to reduce friction and prevent excessive heat from being generated during tapping, which can affect accuracy. It is worth noting that the hole itself must be precisely drilled to the correct diameter corresponding to the size of the tap used.
Tap selection
Choosing the right tap is essential to creating the desired thread quality. Selecting a tap depends on factors such as material, thread size, and specific application. For example, hand taps are often used in manual operations, while machine taps are better suited to the automated processes of CNC machines.
Setting up the CNC machine
In CNC machining, setting up the machine involves designing a fixture to hold the workpiece, aligning the tap with the hole, and programming the machine to perform the tapping operation. The setup must ensure that the tap enters the hole at the correct angle and depth to produce a precise thread.
Performing the tapping
During the tapping process, the tap rotates into the hole to cut the thread. The tap's rotation speed and feed rate must be strictly controlled to prevent tap breakage and ensure thread accuracy. In CNC operations, this step is automated for consistent and repeatable results.
Quality inspection
For parts after tapping, the threads must be inspected to ensure they meet specifications. This includes checking the thread depth, pitch, and overall quality. Any defects will compromise the integrity of the threaded connection, so a thorough inspection is necessary.
Parameters that influence CNC tapping
Several key parameters influence the quality and efficiency of CNC tapping. These factors ensure that threads are cut correctly and extend the life of the tap while keeping the workpiece within the intended specifications.
- Thread size: Determines the size of the thread being cut and matches the specifications of the application.
- Hole diameter: The tap used must fit the diameter of the pre-drilled hole to ensure proper thread engagement.
- Tap: The geometry of the tap, including its flute and tip style, directly affects how the threads are cut.
- Cutting speed: The speed at which the tap rotates affects the smoothness of the cut threads, which in turn affects tool wear.
- Spindle speed: The speed of the machine or drill press that drives the tap during the process is critical to consistent performance.
- Lubrication: Helps reduce friction between the tap and the workpiece, allowing for smoother thread creation and chip evacuation.
The influence of materials on CNC tapping
Materials that are generally easier to CNC tap include: plastics, cast iron, mild steel, aluminum, brass, bronze, red copper, etc. Materials that give CNC tapping considerable difficulty include: titanium, stainless steel, nickel alloys, tungsten alloys, molybdenum alloys, tantalum alloys, etc.
When CNC tapping parts of various materials, it is critical to select materials that can achieve efficient cutting and form well-defined internal threads. These materials must have the right balance of hardness, ductility, elastic modulus, and mechanical properties to support the CNC tapping process. Different materials behave differently under the stress of CNC tapping, so both tap performance and thread quality are affected.
Each material has unique characteristics that affect the ease of thread forming, efficiency, and tool life. Materials are critical to ensuring tool life, thread quality, and efficiency during the manufacturing process. For example, softer metals such as aluminum can increase cutting speeds and reduce tap wear. Harder metals, such as stainless steel and titanium, usually require cutting fluids to reduce friction and heat generation.
CNC Tapping VS CNC Drilling
Tapping is different from drilling. The action of tapping is the process of removing material from the hole wall using a straight fluted multi-point thread cutting tool (tap) to create an internal thread. CNC drilling uses a different tool, usually twist-shaped, and is the process of creating a hole. Usually before tapping, a hole corresponding to the tap diameter needs to be drilled.
CNC Tapping VS Thread Milling
Tapping and thread milling are two different processes used to create threads in a workpiece. Tapping uses a tap with all thread diameters and tooth shapes and cuts the thread while rotating concentrically with the hole. Thread milling, on the other hand, uses a milling cutter with multiple flutes or inserts to create threads. Thread milling is the process of cutting material by spiraling along the desired thread path.
In some applications, tapping is a faster, more direct way to create threads, but there are limitations in terms of thread type, diameter and depth. Thread milling offers greater flexibility and versatility. The choice between tapping and thread milling depends on the specific needs of the machining operation and, most importantly, the expected diameter of the hole to be threaded.
How to Choose the Right CNC Tapping Tool?
The size of a tapping tool, specifically its diameter and pitch, can significantly affect the accuracy of a threading operation, depending on several factors. For example, using an improperly sized tap can result in threads that are too loose or too tight, resulting in poor performance. Proper alignment and centering are also essential to creating straight and accurate threads. If the hole size is too small, it will be difficult to achieve precise alignment. In addition, the relative size of the tap and hole affects the amount of material it engages during the tapping process. Heavier engagement requires more force, which can lead to inaccuracies, tool breakage, or workpiece damage. Selecting a tap of the right length can increase accuracy and is necessary to allow for full depth of thread over the desired area. The size and design of the tapping tool’s flutes or grooves act as chip evacuators during the tapping process, reducing the risk of thread or tool damage. Six key factors to consider when choosing the right tap:
Workpiece Material – Different materials require different taps. Different materials, such as stainless steel, aluminum, or plastic, require different taps due to their different hardness and chip evacuation characteristics. For example, forming taps are great for soft materials like aluminum, while cutting taps are better for harder metals like steel. For harder metal materials like titanium, consider a spiral tip tap for better chip removal.
Thread Size and Depth: The choice of tap depends on the size and depth of the thread being created. Smaller taps are better for shallow holes.
Hole Type (Blind or Through) – For through holes, a spiral tip tap is usually the best choice because it pushes the chips forward. For blind holes, you may want a spiral flute tap for more effective chip evacuation. If you are using a blind hole, use a tap design that can properly handle chip evacuation.
Thread Size and Profile – The thread size and desired thread profile will determine the type of tap you need. Taps for large thread diameters require a more robust design than taps for smaller threads.
Machine or Hand Tapping – Hand taps are used for hand tapping, while machine taps are optimized for high-speed operation on a CNC machine or drill press. Make sure the tap type matches the capacity of the machine being used, whether it is a CNC machine or a drill press. Use rigid tapping for high-speed precision in CNC machining environments. For high-volume production, methods such as multi-spindle tapping or power tapping can significantly reduce cycle time and increase output.
Tapping Speeds – Cutting speed is critical. If you are working at high RPMs, using a rigid tapping method with a machine tap can ensure accuracy and tool life. Lower speeds may be appropriate for manual tapping operations.
Coatings and Treatments – Taps come with various coatings, such as titanium nitride, to reduce friction and increase wear resistance, especially in high-speed applications.
How to Avoid CNC Tapping Errors
Whether you are a professional machinist or an apprentice just starting out, you are likely to encounter certain errors during CNC tapping that will hamper your productivity if you don’t know how to best fix them. Let’s take a look at some of the errors that can occur during CNC tapping and how to better avoid them.
Incorrect Tap Size
Cause: Using a tap size that does not match the hole size or thread specification can result in poor thread quality or damaged parts.
Solution: Always verify the required tap size by referencing the correct tap drilling diagram for the material and thread profile being used. Make sure the tap you use matches the material and thread size of your application. Consider factors such as pitch, hole size, and material hardness.
Incorrect Spindle Speed
Cause: Incorrect spindle speed (too high or too low) can result in poor thread quality and excessive tool wear.
Solution: Adjust the spindle speed based on the material hardness and tap design. Slower speeds are recommended for harder materials, while faster speeds can be tolerated for softer materials. Of course, for plastic materials, the spindle speed cannot be too high, which may generate excessive heat, which in turn can melt plastic parts.
Insufficient lubrication
Cause: No lubrication or insufficient cutting fluid can cause friction, overheating and tool breakage.
Solution: Always use proper lubrication or cutting fluid to reduce heat and wear, improve tap performance and tool life.
Improper alignment
Cause: Misaligned taps can cause threads to cross or break, especially in manual operations.
Solution: Use a tap guide or tapping fixture to ensure proper alignment for accurate and straight threads.
Not removing chips
Cause: Accumulated chips can clog the hole, increase pressure on the tap and may cause breakage.
Solution: Use a spiral tip tap for through holes or a spiral groove tap for blind holes to help evacuate chips during tapping.
Overusing the tap
Cause: Continuing to use a worn tap will result in poor thread quality and potential breakage.
Solution: Regularly check the wear of the tap and replace the tap when there are signs of wear or dullness to maintain high-quality threads.
How much does tapping cost?
The cost of tapping depends on a variety of factors, such as material type, thread complexity, depth, and the equipment used (3-axis\4-axis\5-axis CNC machining center). CNC tapping services typically cost $0.03 to $1.5 per hole. Hard metal materials such as stainless steel or titanium may drive up the price due to increased tool wear and longer processing time. In addition, CNC machining may cost more for tighter tolerances or custom thread profiles. Factors such as labor rates, cutting speeds, and the number of threaded holes also affect pricing. No matter what, Wstitanium is always your first choice. It sounds like low price and high quality are contradictory, but we can always strike a balance that can meet your tolerance requirements while reducing the price to half of our competitors, or even lower. This is due to our 15 years of manufacturing experience and skilled machinists.