Metal Injection Molding Services
Metal Injection Molding (MIM) combines powdered metal with a binder, injects it into a mold, and then heats it to remove the binder and sinter it into a durable part. It is suitable for manufacturing small, complex, and high-precision sputtering targets. It is compatible with a wide range of materials, such as iron-based, nickel alloys, tungsten alloys, titanium alloys, high-temperature alloys, etc.
- 24/7 Engineering Support
- Quality Inspection Report
- Tight tolerance: +/- 0.005mm
- From 1 to 100+ Within 10 Days
- ISO 9001 & ISO 13485 Certificated
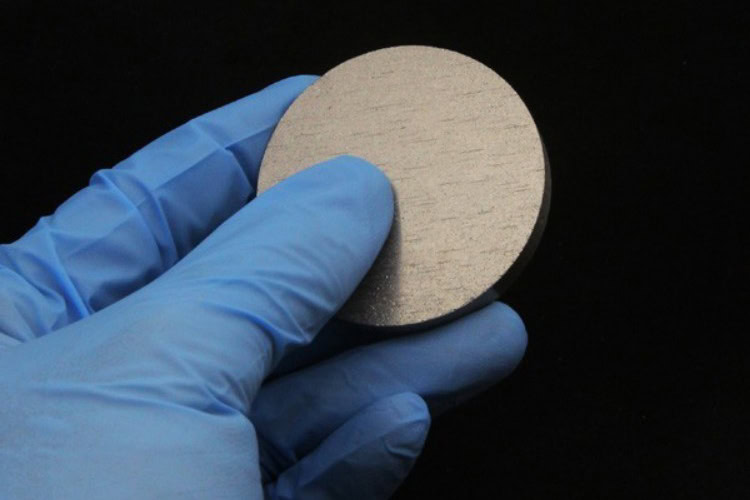
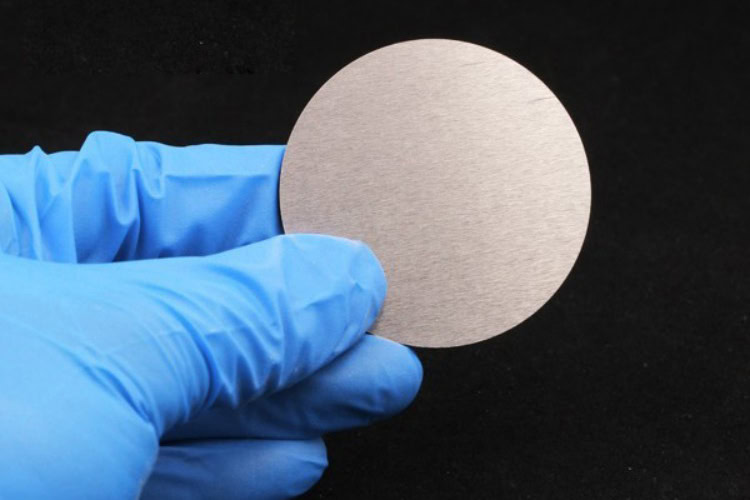
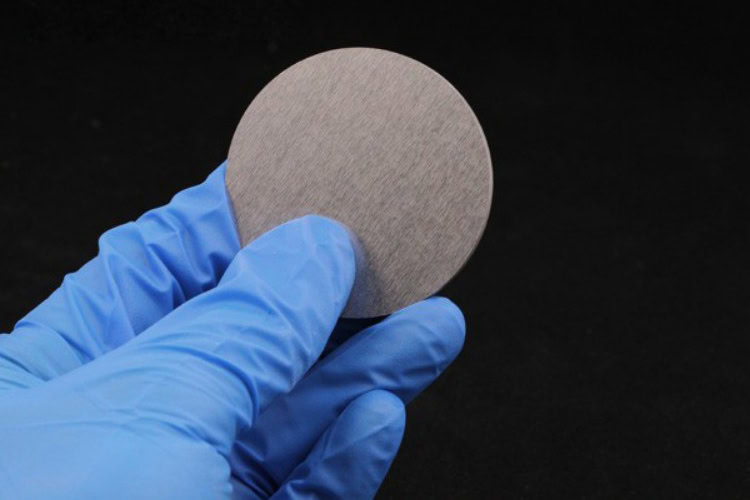
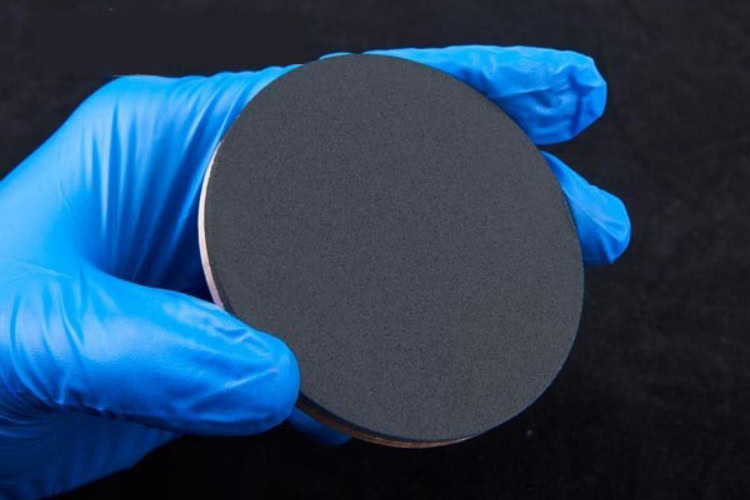
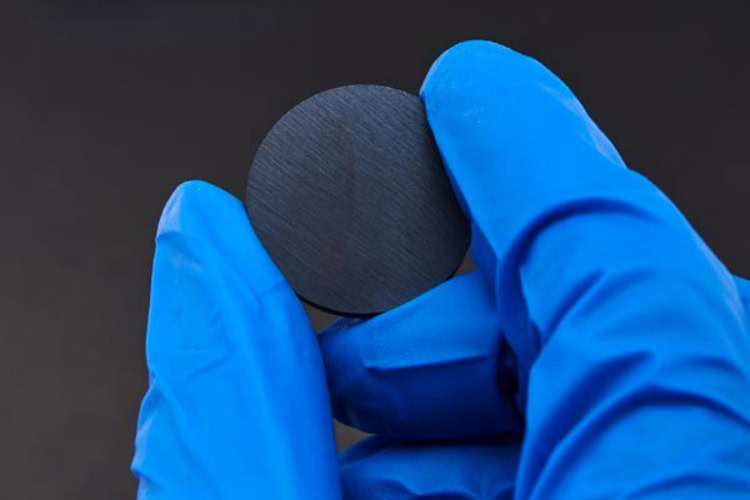
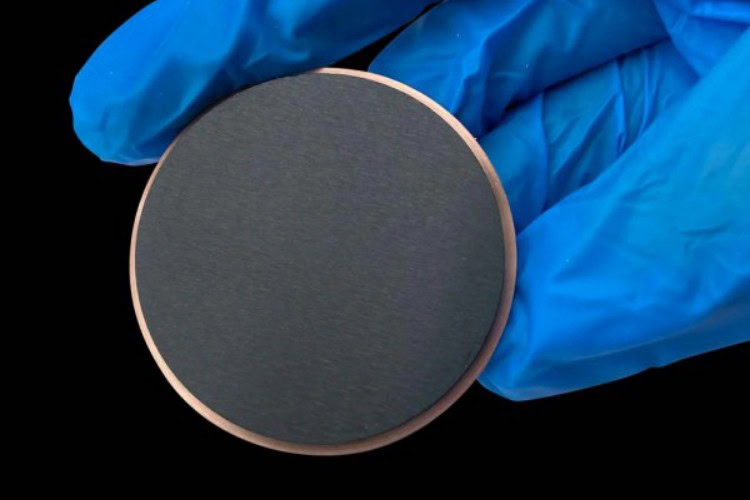
- All uploads are secure and confidential.
Metal Injection Molding Manufacturers for Sputtering Targets
As an advanced parts manufacturing technology, Metal Injection Molding (MIM) is increasingly gaining widespread attention from sputtering target manufacturers. As a well-known metal injection molding manufacturer in China, WSTITANIUN has occupied an important position among China’s sputtering target manufacturers with its excellent technical capabilities, advanced equipment advantages, strong talent team, and significant market advantages.
What is Metal Injection Molding?
Metal injection molding is a new near-net molding process that combines the principle of plastic injection molding with powder metallurgy technology. First, metal powder is evenly mixed with an appropriate amount of organic binder to form an injection feed with good rheological properties; then the feed is injected into the mold cavity through an injection molding machine to form a blank of the desired shape; then the binder in the blank is removed through a degreasing process; finally, the blank is densified through high-temperature sintering to obtain the final metal part. Compared with traditional metal processing methods, metal injection molding technology has many advantages such as the ability to manufacture parts with complex shapes, high dimensional accuracy, good surface finish, high production efficiency, and high material utilization. It is one of the ideal technologies for manufacturing metal sputtering targets.
Metal Injection Molding vs Powder Metallurgy
Metal Injection Molding (MIM)
MIM excels at manufacturing small to medium-sized complex sputtering targets with tight tolerances (±0.1% to ±0.5%) and offers high density (95-98%) and excellent surface finish. MIM is well suited for high-volume manufacturing and is cost-effective for sputtering targets that require minimal post-processing.
Powder Metallurgy (PM)
PM is best suited for larger, simpler-shaped sputtering targets, achieving 90-95% density and tolerances of ±0.5% to ±2%. More finishing work may be required due to lower tooling costs and the ability to process a wide range of materials.
Wstitanium Metal Injection Molding Capabilities
Wstitanium’s continuous R&D investment and teamwork have made major breakthroughs in many key aspects of metal injection molding technology. The new raw material formula developed has significantly improved the performance and quality of sputtering targets; the optimized injection molding process has greatly improved production efficiency while ensuring the high precision and stability of the product; the unique degreasing and sintering technology has effectively solved the defects in traditional processes and further enhanced the competitiveness of sputtering targets.
- Min wall thickness: 0.4 mm
- Min custom part size: 1×2×2 mm
- Max custom part size: 400×400×80 mm
- Min net weight: 0.1g
- Max net weight: 450g
- Cost effective Max weight:100g
- Min tolerance: ± 0.005 mm
- Max Efficiency: 10K pcs per day
- Precision design reference: 0.1%
Precision Mold Manufacturing
The mold is a key tool for metal injection molding, and its quality directly affects the precision and quality of the sputtering target. The mold manufacturing equipment invested by WSTITANIUN includes 5-axis CNC machining centers, EDM machines, and wire cutting machines. The positioning accuracy of the CNC machining center can reach ±0.0005mm, and the repeated positioning accuracy can reach ±0.0005mm, which can produce molds with complex shapes and high precision requirements. For the mold measurement of pure metal sputtering targets, factors such as the shape, size, precision requirements of the target material and the shrinkage rate during the injection molding process are fully considered. The mold material is usually made of high-strength and high-wear-resistant alloy steel, such as Cr12MoV, H13, etc., and is precision machined and heat treated to ensure the dimensional accuracy and surface finish of the mold.
Injection System Optimization
The injection molding equipment inside WSTITANIUN uses high-precision servo motors and advanced hydraulic control technology, which can achieve precise control of injection pressure, injection speed and injection volume. The injection pressure can be precisely adjusted to ±0.1MPa, the injection speed can be controlled with an accuracy of ±0.1mm/s, and the injection volume deviation can be controlled within ±0.01g. This ensures that the feed material is evenly filled in the mold cavity when manufacturing sputtering targets, thereby ensuring the dimensional accuracy and internal quality of the target. For example, for a pure copper sputtering target with a diameter of 100mm, the appropriate injection pressure may be between 50-80MPa, the injection speed is 50-100mm/s, the mold temperature is 60-80℃, the holding pressure is 30-50MPa, and the holding time is 10-20s.
Degreasing
Degreasing is the process of removing the binder and is one of the key links in the manufacture of pure metal sputtering targets by metal injection molding. Parameters such as temperature, time and atmosphere in the degreasing process have an important influence on the degreasing effect and the quality of the blank, and need to be strictly controlled. For example, during the thermal debinding process, the heating rate should not be too fast, so as to avoid cracking of the blank due to the inability to discharge the gas generated by the rapid decomposition of the binder in time; the debinding temperature is generally between 400-800℃, and the debinding time depends on the thickness of the blank and the content of the binder, usually between several hours and tens of hours.
Sintering
Sintering is the process of densifying the debinded blank at high temperature to obtain the final pure metal sputtering target. Parameters such as temperature, time and atmosphere during the sintering process have an important influence on the density, grain size and mechanical properties of the target. For pure metal sputtering targets, vacuum sintering or sintering under the protection of inert gas (argon) is usually used to prevent the metal from oxidizing at high temperatures. The sintering temperature is generally between 0.7-0.9 times the melting point of the metal. For example, the melting point of pure copper is 1083℃, and its sintering temperature may be between 800-950℃. The sintering time depends on the size and shape of the target, generally between 1-5 hours. By optimizing the sintering process parameters, the density and compactness of the target material can be improved to reach or approach the theoretical density, while controlling the growth of the grain size and improving the mechanical properties and sputtering performance of the target material.
Manufacturing pure metal sputtering targets
WSTITANIUN has mastered a series of pure metal sputtering target manufacturing technologies. Ultra-high purity raw materials are used, and the purity and uniformity of the metal are ensured through precise smelting processes. In the process of metal injection molding, the use of self-developed high-precision injection technology can achieve precise control of the size and shape of the target, and the deviation can be controlled within a very small range. At the same time, the unique degreasing and sintering process effectively removes impurities, improves the density and compactness of the target, and makes its performance reach the international leading level. For example, the pure copper sputtering target manufactured has a purity of more than 99.999%, which has been widely used in high-end fields such as semiconductor manufacturing.
Manufacturing alloy sputtering targets
The manufacture of alloy sputtering targets requires precise control of the proportion and distribution of each alloy element, which has extremely high technical requirements. WSTITANIUN has successfully overcome this problem with its deep technical accumulation and innovation capabilities. We use advanced alloy design concepts combined with unique smelting and mixing processes to ensure that the alloy elements are evenly distributed in the target. In the subsequent injection molding, degreasing and sintering processes, the performance of the alloy target is further improved by optimizing the process parameters. For example, a copper indium gallium selenide alloy sputtering target used in solar cell manufacturing has excellent optoelectronic properties and stability, providing strong support for the development of the solar industry.
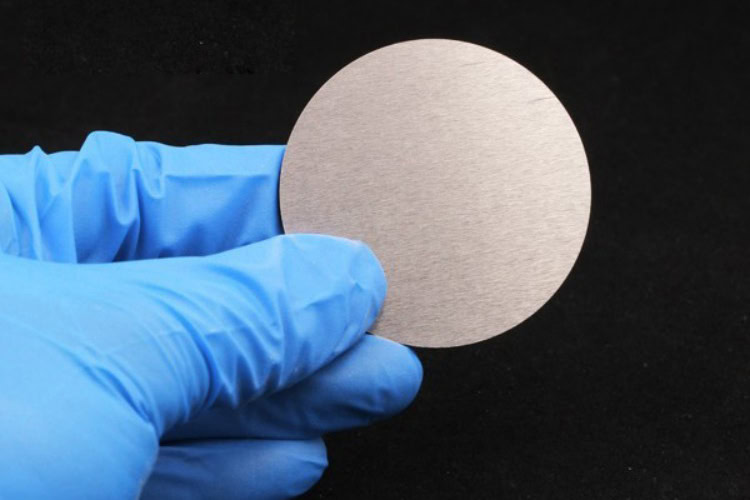
Manufacturing rare earth sputtering targets
Rare earth sputtering targets are extremely difficult to manufacture due to their special physical and chemical properties. WSTITANIUN has a professional rare earth material research team that has conducted in-depth research on the characteristics of rare earth elements. By developing new rare earth raw material pretreatment technology and advanced injection molding technology, the problems of easy oxidation and difficult molding of rare earth targets have been effectively solved. At the same time, in the sintering process, we use a combination of high-temperature vacuum sintering and hot isostatic pressing to significantly improve the quality and performance of rare earth targets. The rare earth sputtering targets manufactured by WSTITANIUN are widely used in high-end fields such as optoelectronics and magnetic materials, providing key material support for the development of related industries.
Finishing Services
Although metal injection molding technology can produce sputtering target blanks with certain precision and quality, the finishing step is essential to meet the strict requirements of various application fields for targets. In order to meet the precise dimensions, precision CNC milling, turning and other processes are used. Secondly, the surface quality has a huge impact on the performance of sputtering targets. CNC grinding can significantly reduce the surface roughness of the target, improve the surface flatness and finish, and ensure the stability of the sputtering process and the uniformity of the film. In addition, through finishing, the internal structure of the target can be optimized, internal stress can be eliminated, and the physical properties and chemical stability of the target can be improved, thereby meeting the stringent requirements in different application scenarios.
CNC Milling Sputtering Targets
CNC Turning Sputtering Targets
CNC Grinding Sputtering Target
Quality Inspection
WSTITANIUN strictly follows the ISO9001:2015 quality management system, from raw materials, manufacturing process, quality inspection, after-sales service. Suppliers are strictly screened and evaluated to ensure that the quality of raw materials meets the requirements. Detailed operating procedures have been formulated to monitor and inspect each process in real time to promptly discover and solve problems. In the quality inspection link, advanced testing equipment and professional testing personnel are equipped to conduct comprehensive testing of sputtering targets and provide you with a comprehensive quality inspection report.
Raw Materials
In order to ensure that the quality composition of raw materials meets the requirements, WSTITANIUN is equipped with advanced material composition analysis equipment, such as X-ray fluorescence spectrometer (XRF), etc. It can quickly and accurately analyze the chemical composition of various metal materials, and the detection accuracy can reach ppm level.
Physical Properties
Measuring instruments, hardness testers, densitometers, thermal expansion meters, etc. can comprehensively test and analyze the mechanical properties (tensile, compression, bending, etc.), hardness, density, thermal expansion coefficient and other physical properties of sputtering targets, providing important data support for the design and application of sputtering targets.
Microstructure
WSTITANIUN is equipped with an X-ray diffractometer (XRD), which can detect the internal crystal structure, defect distribution, phase composition and other information of the sputtering target, and accurately analyze the crystal structure and phase composition of the sputtering target, providing an important basis for quality control and performance optimization.
Metal injection molding combines the flexibility of plastic injection molding with the high-performance advantages of powder metallurgy, bringing revolutionary changes to the manufacture of sputtering targets. Compared with traditional target manufacturing methods, MIM technology can achieve near-net molding of complex-shaped targets, greatly reducing the amount of subsequent processing, and improving material utilization and production efficiency. By precisely controlling the injection molding parameters, the Wstitanium team is able to prepare target blanks with high dimensional accuracy and uniform internal structure. For example, for sputtering targets with special-shaped structures, MIM technology can be used for one-time molding, avoiding the complex operations and material waste of multiple processes in traditional processing methods. At the same time, MIM technology can also achieve composite molding of different materials, providing broad space for the development of new high-performance sputtering targets.