The Ultimate Guide to Ion Plating
This blog will comprehensively review the historical evolution, core concepts, working principles, application scenarios, and technical advantages of ion plating. By comparing it with related technologies such as electroplating, vacuum plating, and PVD, it will deeply analyze its technical characteristics and scope of application, and build a systematic and comprehensive ion plating knowledge system for you.
- Compounds: TiN, TiC, ZrO₂, etc.
- Metals: gold, silver, chromium, titanium, aluminum, etc.
- Alloys: nickel-chromium, cobalt-chromium, titanium-aluminum, etc.
Wstitanium Workshop
Our Powerful Facilities
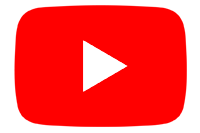
What You Should Know About Ion Plating
In the field of modern industrial manufacturing and materials science, surface modification technology has always played a vital role. Whether pursuing the wear resistance and corrosion resistance of products or improving their decorativeness and functionality, surface coating technology is the core means to achieve these goals. Among the many coating technologies, ion plating has become the “darling” of the high-end manufacturing field due to its unique principle and excellent film performance.
1. Ion Plating History
The development of ion plating technology began in the 1960s. It is a new type of coating technology developed on the basis of vacuum evaporation and sputtering coating combined with glow discharge technology. In 1963, American scientist D. M. Mattox first proposed the concept of ion plating and successfully developed the first ion plating equipment. Early ion plating mainly used DC glow discharge mode to ionize metal vapor and deposit it on the substrate surface. This technology solved the problem of poor film adhesion in traditional evaporation and attracted widespread attention from the industry.
In the 1970s, ion plating technology entered a period of rapid development. Researchers from various countries successively developed different types of ion plating technologies, such as active reaction ion plating (ARE) and hollow cathode ion plating (HCD). Among them, active reaction ion plating successfully prepared compound film layers such as titanium nitride and titanium oxide by introducing reaction gases (such as nitrogen and oxygen), greatly expanding the application range of ion plating.
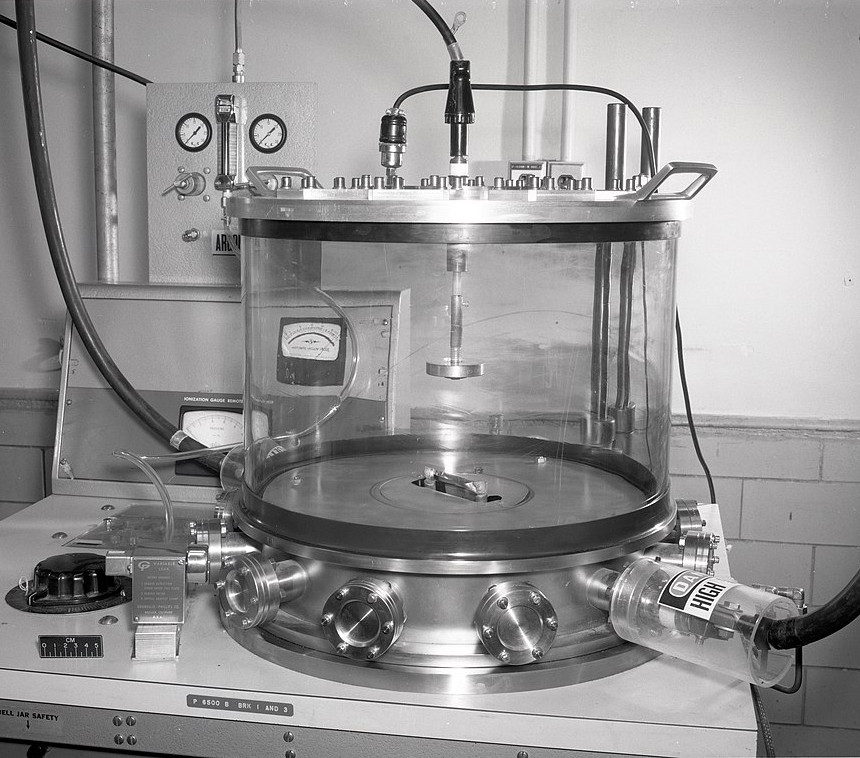
Since the 1980s, ion plating technology has been continuously improved, and new technologies such as medium-frequency magnetron sputtering ion plating and multi-arc ion plating have emerged. These technologies have the characteristics of fast deposition rate, high film quality, and wide range of applicable materials, making ion plating widely used in aerospace, machinery manufacturing, decoration and other fields.
2. Ion Plating Working Principle
Ion plating is a coating technology that uses gas discharge to ionize the coating material under vacuum conditions, and deposits the ions on the substrate surface to form a film layer under the action of an electric field. Compared with traditional coating technology, the core feature of ion plating is that the coating material is in an ion state during the deposition process. These ions have high energy (usually hundreds to thousands of electron volts) and can hit the substrate surface at high speed under the acceleration of the electric field, thereby forming a strong bond with the substrate. Ion plating is divided into many types, such as DC ion plating, radio frequency ion plating, multi-arc ion plating, and magnetron sputtering ion plating.
Establishment of vacuum environment: First, the coating chamber is evacuated to a high vacuum state (usually the vacuum degree is 10⁻³~10⁻⁵Pa) to reduce the interference of gas molecules on the coating process and ensure the quality of the film layer.
Gas discharge and plasma generation: By introducing inert gas (such as argon) or reactive gas (such as nitrogen, oxygen), and applying a high voltage electric field between the substrate and the evaporation source, the gas is glow-discharged to generate plasma. Plasma is an ionized gas composed of electrons, ions, neutral atoms and molecules, with good conductivity and chemical activity.
Evaporation and ionization of coating materials: The coating materials are evaporated into gas-phase atoms or molecules by resistance heating, electron beam heating, arc discharge, etc. These gas-phase particles collide with high-energy electrons and ions in the plasma, and some are ionized into positive ions. At the same time, they may also react chemically with the reactive gas to form compound ions.
Acceleration and deposition of ions: Under the action of the electric field, the positively charged coating ions are accelerated to move toward the negatively charged substrate and hit the substrate surface with higher energy. These ions migrate, diffuse, nucleate and grow on the substrate surface, eventually forming a continuous and dense film layer. At the same time, the bombardment of high-energy ions will also cause a sputtering effect on the substrate surface, removing pollutants and oxide layers on the surface, further improving the adhesion between the film layer and the substrate.
4. Advantages of Ion Plating
The reason why ion plating technology can be widely used in many fields is due to its significant technical advantages, which can be summarized as the following eight points:
1. Strong film adhesion
The bonding strength between the ion-plated film and the substrate is usually 50~300MPa, which is much higher than that of traditional evaporation (5~20MPa) and electroplating (10~50MPa). This is because the high-energy ions diffuse and mix with the substrate surface during the deposition process to form a “metallurgical bonding” transition layer. Even under severe vibration, high temperature or friction conditions, the film is not easy to fall off. For example, after the valve spring of an automobile engine was ion-plated, the film did not peel off in 1 million fatigue tests.
2. High density of the film
The internal porosity is extremely low (usually < 1%), which effectively blocks the intrusion of water, oxygen and corrosive media. For example, the ion-plated TiN coating can resist salt spray corrosion for more than 5,000 hours, while the traditional electroplated chromium is only 1,000 hours. The film layer has fine grains (nanoscale), and its hardness, wear resistance, oxidation resistance and other properties are significantly improved. For example, the friction coefficient of the DLC coating can be as low as 0.05, which is much lower than 0.5 of steel-steel friction.
3. Good uniformity of the film layer
Under the action of the electric field, ions have the ability to migrate to the surface of the substrate (especially complex parts such as grooves and small holes) in a directional manner, achieving a “wrap-around plating” effect, so that workpieces with complex shapes (such as gear tooth surfaces and deep hole inner walls) can obtain uniform film thickness (thickness deviation < 5%). For example, after the inner wall of the gun barrel is ion-plated, the film thickness difference from the muzzle to the tail can be controlled within 0.5μm, while the deviation of electroplating technology is usually more than 10%.
4. A wide range of applicable materials
Ion plating has almost no restrictions on the substrate material. Whether it is metal (steel, aluminum, titanium), ceramic (aluminum oxide, zirconium oxide), glass, or plastic (ABS, PC), composite materials, it can be plated. At the same time, the depositable film materials are also extremely rich, including metals, alloys, ceramics, semiconductors, etc., which can meet different performance requirements (such as conductivity, insulation, wear resistance, biocompatibility, etc.).
5. Small thermal impact on the substrate
The deposition temperature of ion plating is usually 100~500℃ (can be controlled by process adjustment), which is much lower than the phase change or deformation temperature of the substrate (such as aluminum alloy, plastic), and will not cause the substrate performance to deteriorate or change in size. For example, the temperature of plastic parts can be controlled below 80℃ during coating to avoid deformation; after high-precision bearings are coated, the dimensional tolerance change can be controlled within 0.001mm.
6. Excellent environmental performance
Ion plating is carried out in a vacuum environment, without the use of chemical reagents such as electrolytes, acids and alkalis, and will not produce pollutants such as wastewater, waste gas, and waste residues, which solves the environmental protection problems of electroplating and other technologies from the source. At the same time, the utilization rate of coating materials is high (up to 70%~90%), which is much higher than electroplating (30%~50%), reducing material waste. It is suitable for medical, food, electronics and other fields with high requirements on cleanliness.
7. Customizable film performance
The technical parameters of ion plating (such as vacuum, gas flow, discharge power, substrate bias, deposition temperature, etc.) can be precisely controlled to achieve precise control of film composition, structure, thickness (accuracy up to ±0.1μm) and performance. For example, by adjusting the nitrogen flow, different color films from pure titanium (metallic color) to titanium nitride (golden yellow) to titanium aluminum nitride (purple blue) can be prepared; by changing the bias voltage, the hardness of the film can be controlled (adjustable from 1000HV to 4000HV) to meet the needs of different scenarios.
8. Wide range of applicable substrate sizes
Ion plating equipment can be designed as small laboratory equipment (processing precision parts of several millimeters) or large industrial production lines (processing plates and pipes several meters long) according to needs, which can meet the coating needs from microelectronic components to large aviation components. For example, large multi-arc ion plating equipment can process dozens of car wheels at the same time, while small magnetron ion plating equipment can accurately coat semiconductor lead frames with a diameter of 0.1mm….
5. Ion Plating vs. Electroplating
Item | Ion Plating | Electroplating |
Core Principle | Under vacuum environment, coating material ions are accelerated by electric field and deposited on the substrate surface. | Under electrolysis, metal ions are reduced from the electrolyte and deposited on the substrate surface. |
Environmental Requirements | Requires high vacuum system (10⁻³ – 10⁻²Pa), complex equipment and high initial investment. | At room temperature and pressure, it relies on electrolyte and requires treatment of waste water and gas, resulting in large environmental protection investment. |
Substrate Material Compatibility | Metals, ceramics, glasses, plastics, composite materials, etc. can be directly coated. | Only applicable to conductors or semiconductors. Non-conductors need to be treated with conductivity first (such as coating conductive glue). |
Types of Coating Materials | Metals, alloys, compounds (nitrides, oxides, carbides, etc.), diamond-like carbon, etc. | Mainly metals and alloys, difficult to prepare high-purity compound coatings. |
Coating Adhesion | 50 – 300MPa, metallurgical bonding, strong impact and corrosion resistance. | 10 – 50MPa, mainly mechanical bonding, prone to peeling under thermal alternation or stress. |
Coating Density | Density > 99%, porosity < 1%, can block the penetration of corrosive media. | Relatively low density (usually 80% – 90%), prone to pinholes and cracks, requiring multi-layer electroplating to make up for it. |
Uniformity of Complex Shapes | Ions are uniformly deposited under the guidance of electric field, and the thickness deviation of the coating at grooves and small holes is < 5%. | Depends on the convection of electrolyte, and the “tip effect” is prone to occur in complex parts, with a thickness deviation of up to 20% – 50%. |
Deposition Temperature | 50 – 500℃ (adjustable), with little thermal influence on the substrate. | Room temperature (some processes need to be heated to 80 – 100℃), but the electrolyte may corrode the substrate. |
Environmental Protection | No pollutant emission, material utilization rate 70% – 90%. | Produces heavy metal wastewater and acid mist, requiring high environmental protection treatment costs. |
Deposition Rate | 0.5 – 20μm/h (medium rate). | 1 – 50μm/h (fast, but thick films are prone to stress cracking). |
Coating Thickness Range | 0.1 – 100μm (precise control). | 1 – 200μm (thick films are prone to uneven performance). |
Typical Application Scenarios | Aerospace components, high-end tools, precision electronics, medical implants. | Automotive chrome plating parts, hardware decoration, ordinary fasteners, plumbing equipment. |
6. Ion Plating vs. Vacuum Plating
ms | Ion Plating | Vacuum Plating (Taking Vacuum Evaporation Plating and Sputtering Plating as Examples) |
Core Principle | In a vacuum environment, the coating material is ionized, and the ions are accelerated by an electric field to bombard and deposit on the surface of the substrate to form a coating. | Vacuum evaporation plating: Heat the coating material in a vacuum to evaporate it, and the vapor condenses on the surface of the substrate to form a coating; |
Sputtering plating: In a vacuum, high-energy particles bombard the target, causing the target atoms to escape and deposit on the surface of the substrate. | ||
Degree of Ion Participation | The coating material is mainly deposited in the form of ions, and the ionization rate is high (usually above 30%). | Vacuum evaporation plating: Almost no ions are involved, and deposition occurs with neutral atoms/molecules; |
Sputtering plating: Some ions are involved, but the ionization rate is low (generally < 10%). | ||
Bonding Mode Between Substrate and Coating | Mainly metallurgical bonding, with strong bonding force (50 – 300MPa). | Vacuum evaporation plating: Mainly physical adsorption, with weak bonding force (usually < 10MPa); |
Sputtering plating: Moderate bonding force (10 – 50MPa), slightly stronger than evaporation plating. | ||
Bombardment Effect on Substrate | Ions bombard the surface of the substrate, which can clean the surface and generate a certain heating effect to promote interface diffusion. | Vacuum evaporation plating: No bombardment effect, only rely on vapor condensation; |
Sputtering plating: Has a certain bombardment effect, but the intensity is lower than that of ion plating. | ||
Coating Density | Density > 99%, porosity < 1%, excellent corrosion resistance and wear resistance. | Vacuum evaporation plating: Low density, prone to pinholes and pores; |
Sputtering plating: Higher density (85% – 95%), but still slightly lower than ion plating. | ||
Applicable Materials | Can plate metals, alloys, compounds (nitrides, oxides, etc.), diamond-like carbon, etc. | Vacuum evaporation plating: Suitable for low-melting-point metals and some compounds; |
Sputtering plating: Applicable to a wider range of materials, but the preparation of compound coatings is more difficult than that of ion plating. | ||
Substrate Material Compatibility | Good adaptability to various substrates such as metals, ceramics, glass, and plastics. | Vacuum evaporation plating: Better for substrates with poor heat resistance such as plastics (low-temperature deposition); |
Sputtering plating: Applicable to a wide range of substrates, but some sensitive materials may be affected by bombardment. | ||
Deposition Temperature | 50 – 500掳C (adjustable), with little thermal influence on the substrate. | Vacuum evaporation plating: Usually < 100°C (low-temperature deposition is possible); |
Sputtering plating: Generally 50 – 300°C, and the temperature of some processes is higher. | ||
Typical Applications | Aerospace components, high-end tools, medical implants, precision electronic components. | Vacuum evaporation plating: Optical films (such as lens coating), packaging material coatings; |
Sputtering plating: Decorative coatings (such as mobile phone shells), magnetic films, semiconductor films. |
7. Application of Ion Plating
Ion plating technology, with its unique process characteristics, plays an irreplaceable role in various fields of modern industry. Compared with electroplating, it solves the pain points of environmental protection and film adhesion; compared with other vacuum plating technologies, it achieves a leap-forward improvement in performance. As a high-end branch of PVD technology, it leads the development of surface modification technology towards higher precision, higher performance and more environmental protection. Its applications range from high-temperature resistant coatings for aerospace engines to wear-resistant casings for smartphones, from super-hard films that extend tool life to antibacterial coatings that ensure medical safety.
Aerospace
Depositing heat-resistant, wear-resistant, and corrosion-resistant ceramic films (such as zirconium oxide and aluminum oxide) on the surfaces of turbine blades, combustion chambers and other components can improve the high-temperature performance and service life of the components. Depositing low-emissivity films can reduce the infrared radiation characteristics of aircraft and improve stealth performance; depositing wear-resistant coatings to reduce aerodynamic wear.
Mechanical
Depositing superhard films such as titanium nitride (TiN) and titanium carbide (TiC) on the surfaces of high-speed steel and carbide tools can significantly improve the hardness, wear resistance and service life of the tools, and increase cutting efficiency by 30%~50%. Ion plating the surfaces of cold stamping dies, die-casting dies, etc. can improve the wear resistance, corrosion resistance and demolding performance of the molds, and extend the service life of the molds by 2~5 times. Depositing wear-resistant and friction-reducing films (such as diamond-like carbon films DLC) on the surfaces of bearings can reduce the friction coefficient and improve the operating accuracy and service life of the bearings.
Decoration
Depositing titanium nitride (golden yellow) and titanium carbide (black) films on the surface of silver, copper and other substrates not only has a beautiful decorative effect, but also improves the wear resistance and corrosion resistance of jewelry and prevents discoloration. For example, faucets, door handles, lamps, etc., deposit different colored films (such as gold, silver, black) through ion plating, which are not only beautiful and durable, but also increase the added value of the product.
Electronics
Depositing metal film layers (such as aluminum and copper) on the surface of semiconductor chips as electrodes and interconnects, ion plating can ensure the uniformity and conductivity of the film layer. Depositing magnetic film layers (such as cobalt-based alloys) on the surface of magnetic recording materials such as hard disks and magnetic tapes, ion plating can improve the magnetic properties and stability of the film layer. Preparing optical films such as anti-reflection films, reflective films, and filter films for optical lenses, displays and other devices. The optical films prepared by ion plating have good optical properties and stability.
Medical
Depositing antibacterial film layers (such as silver films) on the surface of medical devices such as scalpels and syringes can inhibit bacterial growth and reduce the risk of infection; depositing wear-resistant coatings to increase the service life of medical devices. Depositing a biocompatible film layer (such as hydroxyapatite) on the surface of biological implants such as artificial joints and bone screws can improve the bonding between the implant and human tissue and reduce rejection reactions.
8. Conclusion
After more than 60 years of development, ion plating technology has evolved from an initial laboratory concept to one of the core technologies supporting high-end manufacturing. Its core advantage is that through high-energy ion deposition, it achieves strong bonding between the film layer and the substrate, high density and excellent performance, while taking into account environmental protection and material adaptability. This makes it irreplaceable in fields with high requirements for film performance.