Sputtering Coating
With its unique advantages and wide applicability, sputtering coating has been deeply applied in many fields. From precise metal wiring in microelectronic devices to high-performance coatings on optical components; from high-temperature protective layers in the aerospace field to decorative coatings on daily necessities, sputtering coating technology is everywhere and has a profound impact on the progress of science and technology.
- DC Sputtering
- RF Sputtering
- Reactive Sputtering
- Ion Beam Sputtering
- Magnetron Sputtering
Wstitanium Workshop
Our Powerful Facilities
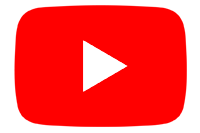
Everything You Should Know About Sputtering Coating
With the rapid development of science and technology, the requirements for material performance are increasing day by day, and sputtering coating technology is also constantly innovating and improving. New sputtering methods are constantly emerging. The options for coating materials are more abundant and diverse. The accuracy and stability of technical control have been greatly improved. This enables sputtering coating to not only meet the needs of traditional fields, but also provide key thin film preparation solutions for emerging technology fields such as quantum computing, flexible electronics, biomedical engineering, etc.
What is sputtering coating?
Sputtering coating is a physical vapor deposition (PVD) technology. Its basic principle is to bombard the target surface with high-energy ions (usually argon ions Ar⁺) in a vacuum environment, so that the target atoms gain enough energy to overcome the surface binding force and escape. These escaped atoms are deposited on the substrate surface and gradually form a thin film. This process involves complex physical phenomena, including ion generation, ion acceleration, momentum transfer, and atomic deposition.
Sputtering Working Mechanism
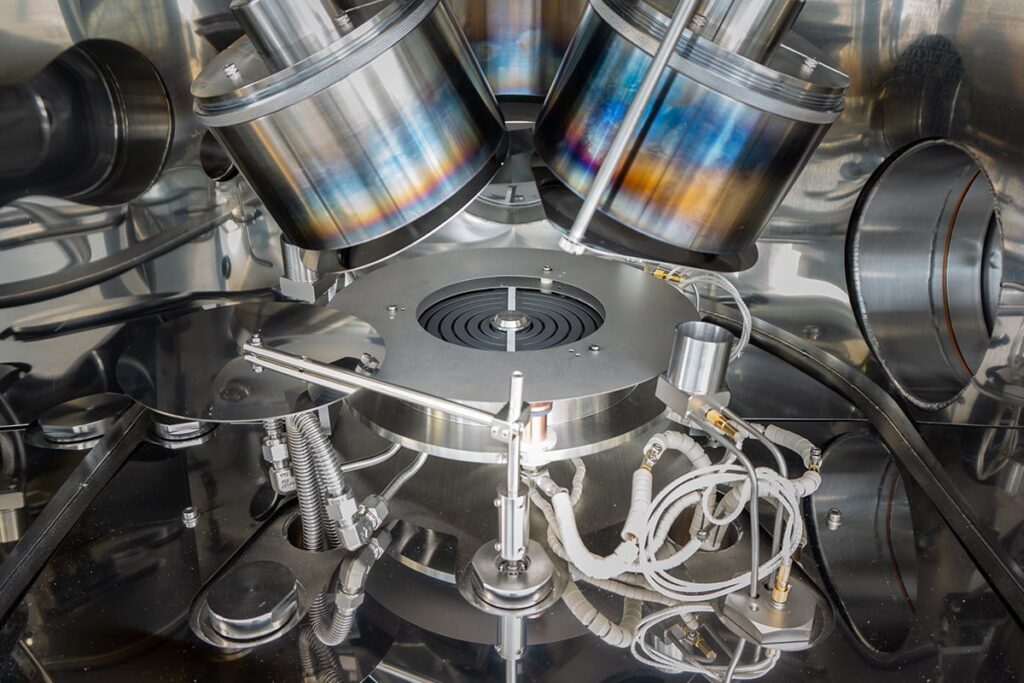
Ion generation and acceleration: Inert gas (such as argon) is introduced into the vacuum chamber, and the gas is ionized by applying an electric field (usually using glow discharge) to generate plasma, which contains a large number of argon ions and free electrons. Argon ions are accelerated under the action of the electric field and obtain higher kinetic energy. For example, in a DC sputtering device, a DC voltage is applied between the target (cathode) and the anode to form an electric field, which accelerates the argon ions to fly toward the target.
Momentum transfer and atomic sputtering: When argon ions with high kinetic energy bombard the target surface, they collide elastically or inelastically with the target atoms, transferring their own kinetic energy to the target atoms. When the energy obtained by the target atoms exceeds their binding energy in the lattice, they will sputter out from the target surface. In elastic collisions, ions collide directly with target atoms and transfer kinetic energy instantly; in inelastic collisions, multiple energy exchanges are used to gradually allow the target atoms to obtain enough energy and sputter.
Atomic deposition and film growth: The atoms sputtered from the target are transported in a vacuum chamber in a gaseous form and deposited on the substrate surface. These atoms adsorb and diffuse on the substrate surface, gradually forming atomic clusters. As the number of deposited atoms increases, the clusters continue to grow and connect to each other, eventually forming a continuous film. The growth process of the film is affected by many factors, such as the deposition rate of atoms, substrate temperature, and the diffusion ability of atoms on the substrate surface.
Sputtering vs. Evaporation
Evaporation is the process of evaporating the coating material by heating it, and then the vapor condenses on the substrate surface to form a film. Compared with sputtering, evaporation usually has a higher deposition rate, but poorer coverage of complex-shaped substrates. Because the movement direction of the evaporated atoms is mainly straight, it is difficult to evenly cover all parts of the substrate. In addition, evaporation has limited selectivity for materials, and some high-melting-point materials are difficult to coat. Sputtering can be carried out at a lower temperature and is suitable for temperature-sensitive substrate materials. The sputtered particles have higher energy and can interact strongly with the substrate surface, so that the film has good adhesion to the substrate.
Sputtering vs. CVD
CVD uses gaseous chemicals to react chemically under high temperature and catalysts to generate solid substances and deposit them on the substrate surface to form thin films. CVD can produce high-quality films and can precisely control the chemical composition and crystal structure of the film. However, CVD usually requires a high temperature environment, which may damage the substrate material and may introduce impurities during the reaction process. Sputtering coating does not require high temperature chemical reactions, avoiding the problems caused by high temperature and chemical reactions. It can achieve coating of almost all solid materials, and the equipment is relatively simple and the cost is low.
History of Sputtering Coating
The development of sputtering coating technology is a history of scientific and technological progress full of innovation and breakthroughs. Its origin can be traced back to the 19th century. In 1852, German physicist William Grove observed the sputtering phenomenon for the first time. When he was conducting a gas discharge experiment, he found that when ions bombarded the surface of a metal electrode, metal atoms would detach from the electrode surface and deposit on the surrounding objects. This accidental discovery laid the foundation for the birth of sputtering coating technology.
Early Development Stage
In the decades after Grove discovered the sputtering phenomenon, scientists conducted in-depth research on the basic principles and characteristics of sputtering. In 1902, German scientist Eugen Goldstein further studied the sputtering process and revealed the relationship between the emission mechanism of sputtering atoms and factors such as ion energy and target material. These early studies provided a theoretical basis for the practical application of sputtering coating technology, but due to the limitations of technical conditions at the time, sputtering coating could not be achieved in large-scale industrial production.
Technological Breakthroughs
In the mid-20th century, with the development of vacuum technology, power technology and materials science, sputtering coating technology has made major breakthroughs. The emergence of RF sputtering technology has solved the problem of sputtering coating of insulating materials, which has greatly expanded the application scope of sputtering coating technology. RF sputtering uses the alternating electric field generated by the RF power supply to ionize the gas, thereby realizing the sputtering of insulating target materials. This technology has been widely used in fields such as integrated circuits.
Modern Development Trend
In the 21st century, with the continuous advancement of science and technology, sputtering coating technology has continued to make progress in improving coating quality, reducing costs, and expanding application areas. New sputtering technologies such as pulsed DC sputtering and high-power pulsed magnetron sputtering (HiPIMS) continue to emerge. Pulsed DC sputtering reduces the formation of an insulating layer on the surface of the target material by superimposing high-frequency pulses on the DC voltage, alleviates the target material poisoning phenomenon, and improves the stability and quality of the coating. HiPIMS can generate plasma with a high ionization rate and prepare thin films with excellent performance, showing great application potential in high-end optical films, superhard coatings and other fields.
Sputtering Coating Type
DC Sputtering
DC sputtering is a technology that uses ions generated by DC glow discharge to bombard the target material for sputtering coating. DC sputtering is relatively low in cost and is suitable for large-area uniform coating. However, it also has some limitations. Since DC sputtering requires the target material to have good conductivity, it can only be used for coating conductive materials, and cannot be used for insulating materials.
RF Sputtering
RF sputtering is a technology that uses positive ions in RF discharge plasma to bombard the target material, sputter out target atoms and deposit them on the surface of a grounded substrate. RF sputtering can be used to deposit thin films of almost any solid material, including conductors, semiconductors and insulators. The thin films it obtains are dense, high in purity and firmly attached to the substrate.
Ion Beam Sputtering
Ion beam sputtering is a technology that uses an independent ion source to generate a high-energy ion beam, directly bombarding the target surface, so that the target atoms are sputtered out and deposited on the substrate to form a thin film. The ion source usually uses a Kaufman ion source or a radio frequency ion source to accelerate the ions to a higher energy.
Reactive Sputtering
Reactive sputtering is a technology in which reactive gases (such as oxygen, nitrogen, methane, etc.) are introduced into the vacuum chamber during the sputtering process to react chemically with the sputtered target atoms to form a compound film on the substrate surface. Reactive sputtering is widely used in the preparation of various compound films, such as oxides, nitrides, carbides, etc.
Magnetron Sputtering
Magnetron sputtering is a technology that establishes a racetrack magnetic field on the cathode target surface, uses it to control the movement of secondary electrons, prolongs their residence time near the target surface, increases the probability of collision with the gas, and thus increases the plasma density. It can be carried out at a lower working pressure.
Pulse DC Sputtering
Pulse DC sputtering is to superimpose high-frequency pulses on the basis of DC voltage. Its power supply periodically outputs pulse signals while providing stable DC output to reduce target poisoning. Pulse DC sputtering is suitable for reactive sputtering processes and can effectively improve the stability of the coating process and the quality of the film. It reduces impurities and defects in the film.
Sputtering Yield
Sputtering yield, also known as sputtering coefficient, refers to the average number of target atoms sputtered from the target surface by each incident ion during the sputtering process, usually represented by Y. It is an important parameter for measuring the efficiency of sputtering coating, which directly affects the deposition rate and preparation cost of the film. The energy of sputtered atoms varies greatly, and usually the kinetic energy of these atoms exceeds tens of electron volts (usually 600 eV). About one percent of the ions hit the target surface with ballistic impact and return to the substrate, resulting in re-sputtering. The size of the sputtering yield depends on many factors, including the energy and type of the incident ions, the properties of the target (such as atomic mass, crystal structure, binding energy, etc.), and the working conditions during sputtering (such as gas pressure, temperature, etc.).
Table 1. Sputtering Yield of Different Materials for 600 eV Ion Energy
Sputtering Coating Material Options
The choice of sputtering materials, as the core element of magnetron sputtering, directly determines the properties and application range of the film. Different sputtering materials, due to their unique physical, chemical and electrical properties, can produce films with different functions and characteristics. For example, metal materials are often used to prepare conductive films, metal decorative films and wear-resistant coatings in electronic devices due to their good conductivity, high sputtering rate and excellent mechanical properties; alloy materials can obtain films with special properties by cleverly adjusting the proportion of different metal elements, such as high strength, high corrosion resistance or special electrical and magnetic properties, and are widely used in high-end fields such as aerospace and automobile manufacturing; ceramic materials, with their high hardness, high temperature resistance and strong chemical stability, perform well in the preparation of optical films, insulating films and protective coatings, providing strong support for the performance improvement of optical instruments and electronic equipment.
Aluminum (Al) Sputtering Target
Aluminum is a widely used sputtering metal material. It has low density and good electrical conductivity. Its density is about 2.7g/cm³, and its room temperature conductivity can reach 3.77×10⁷S/m. In the field of electronic devices, aluminum is often used to prepare metal wiring in integrated circuits. Aluminum films are widely used in optical instruments such as telescopes and microscopes.
Copper (Cu) Sputtering Target
Copper has excellent electrical conductivity, with an electrical conductivity of up to 5.96×10⁷S/m. In ultra-large-scale integrated circuits, copper has gradually replaced aluminum as the mainstream metal wiring material due to its low resistance characteristics. Copper also has good thermal conductivity and good electrical conductivity, and effectively shields electromagnetic interference.
Gold (Au) Sputtering Target
Gold has extremely high chemical stability, hardly reacts chemically with other substances, and can maintain good performance in various harsh environments. Its good conductivity and oxidation resistance make it an ideal coating material for key parts in electronic devices. In the jewelry industry, sputtering gold film can achieve a gold-like decorative effect on the surface of other metals or materials.
Silver (Ag) Sputtering Target
Silver has the highest conductivity among all metals, with an electrical conductivity of 6.30×10⁷S/m. Silver film has very high reflectivity in the visible and near-infrared bands and is widely used to make high-quality reflectors. Silver also has good antibacterial properties, which makes it uniquely used in biomedicine and food packaging. However, the chemical stability of silver is relatively poor.
Titanium (Ti) Sputtering Target
Titanium has a high melting point (1668℃) and good mechanical properties. Its density is 4.506g/cm³, that is, the ratio of strength to density is large. Sputtering titanium film can improve the wear resistance, corrosion resistance and high temperature resistance of parts. Titanium also has excellent biocompatibility. Titanium film can also be used for anti-corrosion coatings.
Chromium (Cr) Sputtering Target
Chromium has a high hardness, Mohs hardness of about 9, and good wear resistance. Sputtering chromium film significantly improves the surface hardness and wear resistance of parts. Chromium also has good corrosion resistance and can remain stable in a variety of chemical environments. Chromium film has a bright metallic appearance and is often used for surface decoration.
Nickel (Ni) Sputtering Target
Nickel has good corrosion resistance and can remain stable in many chemical media and is not easily corroded. Nickel film can be used to enhance the mechanical strength and reliability of components, and its good conductivity also helps the transmission of electronic signals. Nickel-based alloy films are widely used in the manufacture of storage media such as hard disks and magnetic tapes.
Tungsten (W) Sputtering Target
Tungsten has an extremely high melting point of 3422℃, one of the highest melting points of all metals. This makes it have excellent stability in high temperature environments. Sputtered tungsten film can be used as a high temperature protective coating. Sputtered tungsten film can be used to coat tools to improve the cutting performance and service life of the tools.
Molybdenum (Mo) Sputtering Target
Molybdenum has good high-temperature performance and can still maintain high strength and stability at high temperatures. Molybdenum is one of the important materials for manufacturing thin-film transistors (TFTs). Sputtered molybdenum film is used as the electrode and wiring material of TFTs. In the field of solar cells, molybdenum film is used as the back electrode material.
Tantalum (Ta) Sputtering Target
Tantalum has excellent chemical stability and shows good corrosion resistance in most chemical media, especially in highly corrosive acid and alkali environments. Sputtered tantalum film can provide reliable corrosion protection. Tantalum also has good biocompatibility. Sputtered tantalum film is also used to manufacture electrode materials for tantalum capacitors.
Niobium (Nb) Sputtering Target
Sputtering niobium film can be used to prepare superconducting thin films for the manufacture of superconducting quantum interference devices (SQUIDs), superconducting filters, etc. These devices play a key role in biomedical detection, communications, quantum computing, etc. The corrosion resistance of niobium makes it a corrosion-resistant coating material.
Palladium (Pd) Sputtering Target
Palladium has good catalytic properties and is used as a catalyst. Sputtering palladium film on the surface of the carrier material increases the surface area of palladium and improves the catalytic activity. Palladium is often used to make electrodes and connecting materials for electronic components. Sputtering palladium film achieves decorative effects on other metal surfaces.
Platinum (Pt) Sputtering Target
Platinum has extremely high chemical stability and catalytic activity. In the field of fuel cells, platinum catalysts are one of the core materials of proton exchange membrane fuel cells (PEMFC). In the field of electronic devices, platinum is often used to make high-end electronic components, such as electrodes and resistors in integrated circuits.
Rhodium (Rh) Sputtering Target
Rhodium has good catalytic and antioxidant properties. Many important chemical reactions (such as hydrogenation and dehydrogenation reactions in organic synthesis) require the participation of rhodium catalysts. By sputtering rhodium film on the surface of the catalyst carrier, the dispersion and catalytic activity of rhodium can be improved, and the chemical reaction can be promoted.
Iridium (Ir) Sputtering Target
Iridium has an extremely high melting point (2446℃) and chemical stability. Sputtered iridium film can provide excellent high temperature protection and corrosion resistance. Iridium is often used to manufacture high-end electronic components, such as electrodes and interconnect materials in integrated circuits. Iridium is also an important material for making reference electrodes.
Ruthenium (Ru) Sputtering Target
Sputtering ruthenium film on the surface of the catalyst carrier achieves more efficient and environmentally friendly chemical production. Ruthenium is also commonly used to manufacture electronic components such as resistors and capacitors. Sputtering ruthenium film or related ruthenium compound film can optimize the photoelectric conversion performance of the battery.
Cobalt (Co) Sputtering Target
Cobalt has good magnetic properties and is one of the important elements for making permanent magnetic materials. Sputtered cobalt film can prepare high-performance permanent magnetic films for micro motors, micro speakers, etc. Cobalt is also commonly used to manufacture metal interconnect materials in integrated circuits. Cobalt-based alloys have certain biocompatibility.
Zinc (Zn) Sputtering Target
Zinc has good corrosion resistance. Sputtering zinc film on the surface of steel to form a galvanized layer is a common method for steel corrosion protection. It is widely used in construction, automobiles, bridges and other fields. Zinc is the negative electrode material of common batteries such as zinc-manganese batteries and zinc-air batteries. Zinc film is also used in the field of decoration.
Add Your Heading Text Here
Lorem ipsum dolor sit amet, consectetur adipiscing elit. Ut elit tellus, luctus nec ullamcorper mattis, pulvinar dapibus leo.
Add Your Heading Text Here
Lorem ipsum dolor sit amet, consectetur adipiscing elit. Ut elit tellus, luctus nec ullamcorper mattis, pulvinar dapibus leo.
Add Your Heading Text Here
Lorem ipsum dolor sit amet, consectetur adipiscing elit. Ut elit tellus, luctus nec ullamcorper mattis, pulvinar dapibus leo.
Add Your Heading Text Here
Lorem ipsum dolor sit amet, consectetur adipiscing elit. Ut elit tellus, luctus nec ullamcorper mattis, pulvinar dapibus leo.
Add Your Heading Text Here
Lorem ipsum dolor sit amet, consectetur adipiscing elit. Ut elit tellus, luctus nec ullamcorper mattis, pulvinar dapibus leo.
Add Your Heading Text Here
Lorem ipsum dolor sit amet, consectetur adipiscing elit. Ut elit tellus, luctus nec ullamcorper mattis, pulvinar dapibus leo.
Add Your Heading Text Here
Lorem ipsum dolor sit amet, consectetur adipiscing elit. Ut elit tellus, luctus nec ullamcorper mattis, pulvinar dapibus leo.
Add Your Heading Text Here
Lorem ipsum dolor sit amet, consectetur adipiscing elit. Ut elit tellus, luctus nec ullamcorper mattis, pulvinar dapibus leo.
Add Your Heading Text Here
Lorem ipsum dolor sit amet, consectetur adipiscing elit. Ut elit tellus, luctus nec ullamcorper mattis, pulvinar dapibus leo.
Add Your Heading Text Here
Lorem ipsum dolor sit amet, consectetur adipiscing elit. Ut elit tellus, luctus nec ullamcorper mattis, pulvinar dapibus leo.
Add Your Heading Text Here
Lorem ipsum dolor sit amet, consectetur adipiscing elit. Ut elit tellus, luctus nec ullamcorper mattis, pulvinar dapibus leo.
Add Your Heading Text Here
Lorem ipsum dolor sit amet, consectetur adipiscing elit. Ut elit tellus, luctus nec ullamcorper mattis, pulvinar dapibus leo.
Add Your Heading Text Here
Lorem ipsum dolor sit amet, consectetur adipiscing elit. Ut elit tellus, luctus nec ullamcorper mattis, pulvinar dapibus leo.
Add Your Heading Text Here
Lorem ipsum dolor sit amet, consectetur adipiscing elit. Ut elit tellus, luctus nec ullamcorper mattis, pulvinar dapibus leo.
Add Your Heading Text Here
Lorem ipsum dolor sit amet, consectetur adipiscing elit. Ut elit tellus, luctus nec ullamcorper mattis, pulvinar dapibus leo.
Add Your Heading Text Here
Lorem ipsum dolor sit amet, consectetur adipiscing elit. Ut elit tellus, luctus nec ullamcorper mattis, pulvinar dapibus leo.
Add Your Heading Text Here
Lorem ipsum dolor sit amet, consectetur adipiscing elit. Ut elit tellus, luctus nec ullamcorper mattis, pulvinar dapibus leo.
Add Your Heading Text Here
Lorem ipsum dolor sit amet, consectetur adipiscing elit. Ut elit tellus, luctus nec ullamcorper mattis, pulvinar dapibus leo.
Add Your Heading Text Here
Lorem ipsum dolor sit amet, consectetur adipiscing elit. Ut elit tellus, luctus nec ullamcorper mattis, pulvinar dapibus leo.
Add Your Heading Text Here
Lorem ipsum dolor sit amet, consectetur adipiscing elit. Ut elit tellus, luctus nec ullamcorper mattis, pulvinar dapibus leo.
Add Your Heading Text Here
Lorem ipsum dolor sit amet, consectetur adipiscing elit. Ut elit tellus, luctus nec ullamcorper mattis, pulvinar dapibus leo.
Add Your Heading Text Here
Lorem ipsum dolor sit amet, consectetur adipiscing elit. Ut elit tellus, luctus nec ullamcorper mattis, pulvinar dapibus leo.
Add Your Heading Text Here
Lorem ipsum dolor sit amet, consectetur adipiscing elit. Ut elit tellus, luctus nec ullamcorper mattis, pulvinar dapibus leo.
Add Your Heading Text Here
Lorem ipsum dolor sit amet, consectetur adipiscing elit. Ut elit tellus, luctus nec ullamcorper mattis, pulvinar dapibus leo.
Add Your Heading Text Here
Lorem ipsum dolor sit amet, consectetur adipiscing elit. Ut elit tellus, luctus nec ullamcorper mattis, pulvinar dapibus leo.
Add Your Heading Text Here
Lorem ipsum dolor sit amet, consectetur adipiscing elit. Ut elit tellus, luctus nec ullamcorper mattis, pulvinar dapibus leo.
Add Your Heading Text Here
Lorem ipsum dolor sit amet, consectetur adipiscing elit. Ut elit tellus, luctus nec ullamcorper mattis, pulvinar dapibus leo.
Add Your Heading Text Here
Lorem ipsum dolor sit amet, consectetur adipiscing elit. Ut elit tellus, luctus nec ullamcorper mattis, pulvinar dapibus leo.
Add Your Heading Text Here
Lorem ipsum dolor sit amet, consectetur adipiscing elit. Ut elit tellus, luctus nec ullamcorper mattis, pulvinar dapibus leo.
Add Your Heading Text Here
Lorem ipsum dolor sit amet, consectetur adipiscing elit. Ut elit tellus, luctus nec ullamcorper mattis, pulvinar dapibus leo.
Add Your Heading Text Here
Lorem ipsum dolor sit amet, consectetur adipiscing elit. Ut elit tellus, luctus nec ullamcorper mattis, pulvinar dapibus leo.
Add Your Heading Text Here
Lorem ipsum dolor sit amet, consectetur adipiscing elit. Ut elit tellus, luctus nec ullamcorper mattis, pulvinar dapibus leo.
Add Your Heading Text Here
Lorem ipsum dolor sit amet, consectetur adipiscing elit. Ut elit tellus, luctus nec ullamcorper mattis, pulvinar dapibus leo.
Add Your Heading Text Here
Lorem ipsum dolor sit amet, consectetur adipiscing elit. Ut elit tellus, luctus nec ullamcorper mattis, pulvinar dapibus leo.
Add Your Heading Text Here
Lorem ipsum dolor sit amet, consectetur adipiscing elit. Ut elit tellus, luctus nec ullamcorper mattis, pulvinar dapibus leo.
Add Your Heading Text Here
Lorem ipsum dolor sit amet, consectetur adipiscing elit. Ut elit tellus, luctus nec ullamcorper mattis, pulvinar dapibus leo.
Add Your Heading Text Here
Lorem ipsum dolor sit amet, consectetur adipiscing elit. Ut elit tellus, luctus nec ullamcorper mattis, pulvinar dapibus leo.
Add Your Heading Text Here
Lorem ipsum dolor sit amet, consectetur adipiscing elit. Ut elit tellus, luctus nec ullamcorper mattis, pulvinar dapibus leo.
Add Your Heading Text Here
Lorem ipsum dolor sit amet, consectetur adipiscing elit. Ut elit tellus, luctus nec ullamcorper mattis, pulvinar dapibus leo.