Cathodic Protection Anodes Manufacturer and Supplier In China
Wstitanium has broad application prospects and development potential in the field of cathodic protection anode manufacturing. Through continuous optimization of material properties, innovative manufacturing technology, strict quality control and attention to future development trends, Wstitanium will provide more reliable, efficient, intelligent and environmentally friendly solutions for corrosion protection of metal structures.
- Zinc Sacrificial Anode
- Aluminum Sacrificial Anode
- Magnesium Sacrificial Anode
- High Silicon Cast Iron Anode
- ICCP Anodes
- Graphite Anode
- DSA MMO Anode
- Reference Electrodes
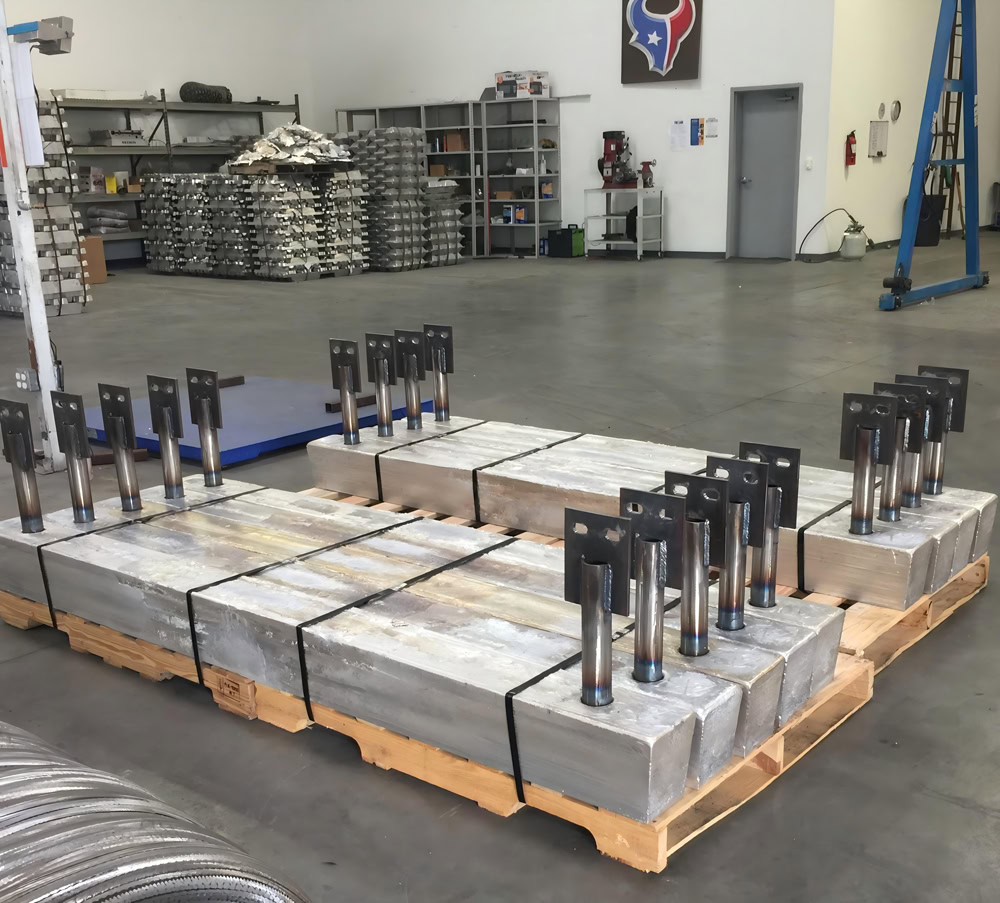
One Stop Cathodic Protection Anodes Factory - Wstitanium
Cathodic protection is an effective technology to prevent metal corrosion, which is widely used in many fields such as oil, natural gas, marine engineering, municipal facilities, etc. In the cathodic protection system, the anode plays a vital role, which directly affects the effect, service life and cost. Wstitanium has shown unique advantages in the field of cathodic protection anode manufacturing.
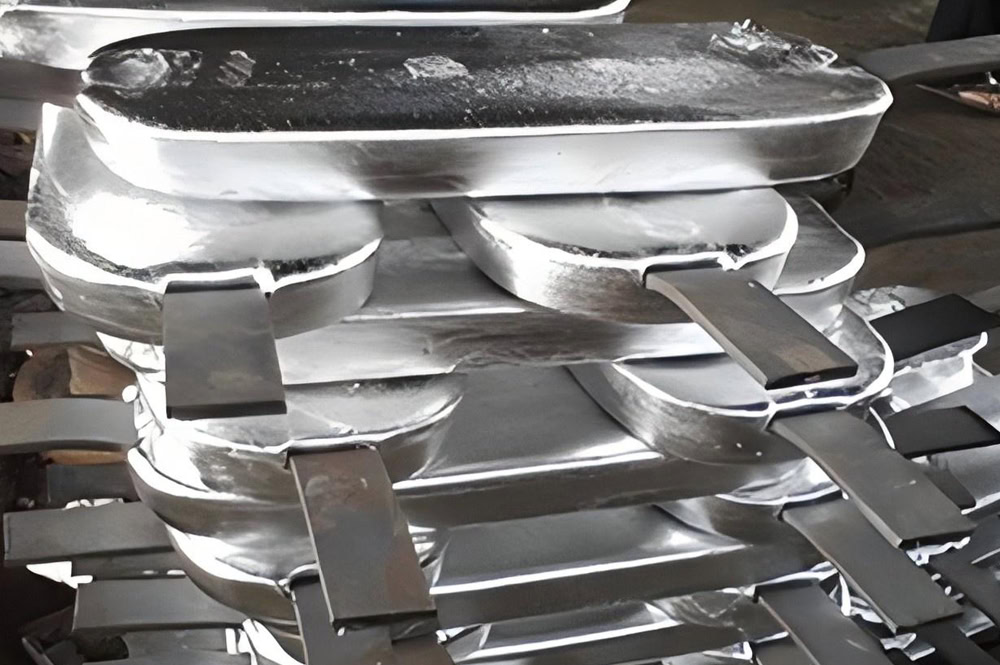
The potential is moderate, the current efficiency is high (up to 90%), the dissolution is uniform, the performance is stable, and it is environmentally friendly. It is widely used in cathodic protection of ships, marine engineering and port facilities in seawater and fresh water media, as well as pipelines and other facilities in low resistivity soil. It is not suitable for high resistivity environments.
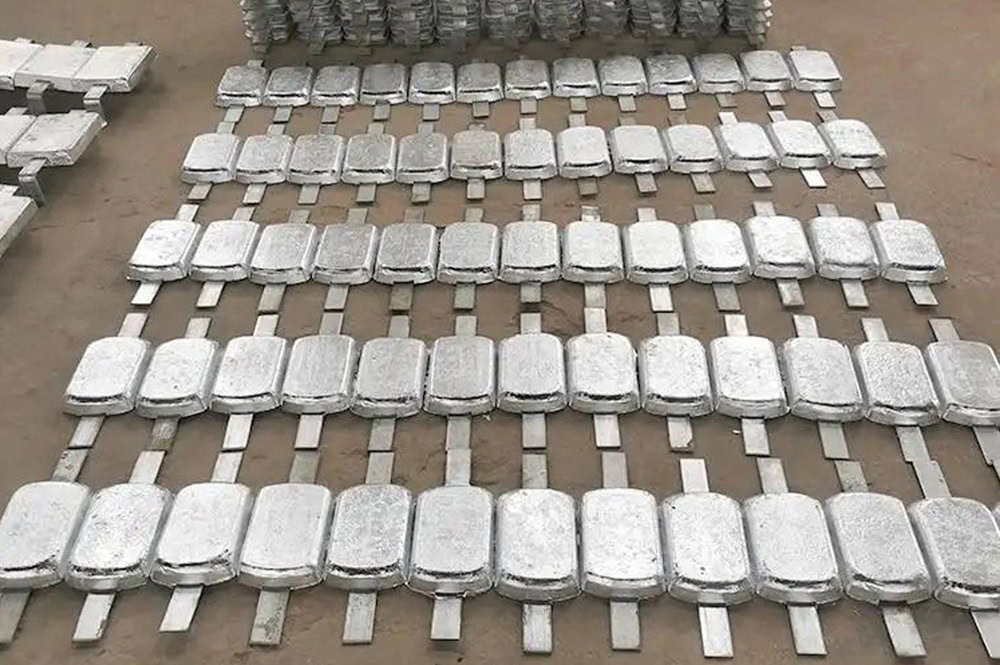
It has good performance in seawater and chloride ion-containing media, and has strong self-regulation ability of the emitted current. It is suitable for the protection of large marine engineering structures, ships, and the inner wall of storage tanks. It has a low density and a large theoretical capacitance, but its performance is greatly affected by alloy composition and environmental factors.
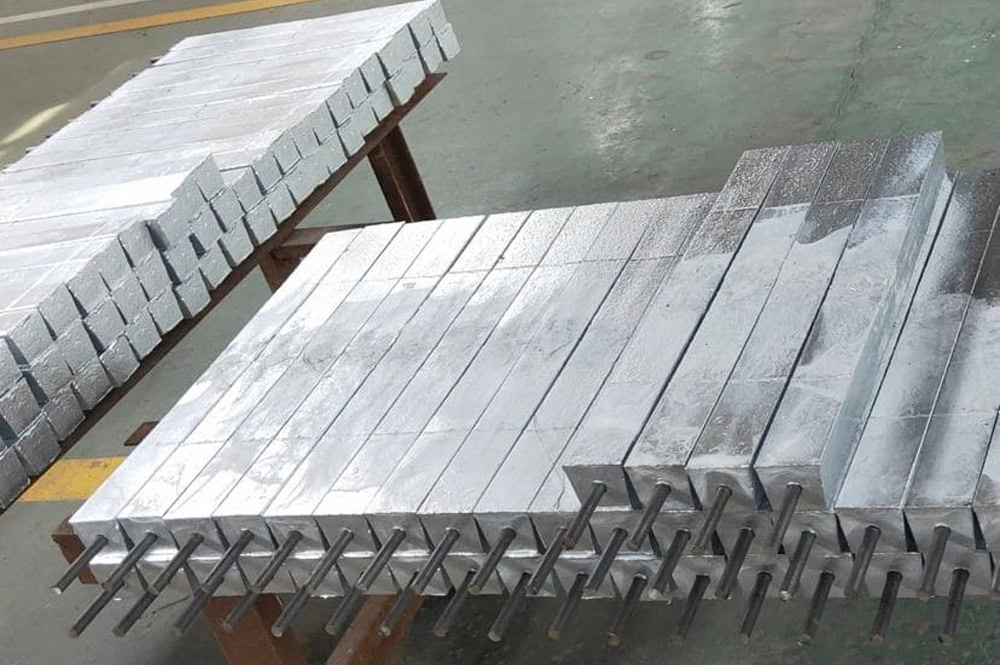
The potential is very negative, the driving voltage is high, and it is suitable for environments with high resistivity such as soil and fresh water, such as the protection of buried pipelines and small underground storage tanks. Its theoretical capacitance is large, but the actual current efficiency is relatively low (generally 50% – 60%), and self-dissolution and other phenomena will occur.
The titanium substrate is coated with a thin layer of a mixture of metal oxides such as platinum, ruthenium, and iridium. ICCP Anodes conduct current from the auxiliary anode into the electrolyte (such as seawater), making the protected metal structure a cathode, forming a negative charge on its surface, and inhibiting the corrosion reaction of the metal.
DSA metal oxide anode is a titanium substrate with an active coating such as ruthenium oxide (RuO₂) and iridium oxide (IrO₂) on the surface. These oxides have good electrocatalytic activity, conductivity and oxidation resistance, which can reduce the overpotential of the electrode reaction and improve the electrolysis efficiency.
Reference Electrodes
The core role of the reference electrode in the field of metal corrosion protection is to provide a stable potential reference for monitoring and regulating the corrosion state of the metal structure to ensure the effectiveness of the cathodic protection system. Multi-point potential measurement locates high corrosion risk points.
Basic Principles of Cathodic Protection
Metal corrosion is mostly an electrochemical process. Take steel as an example. In a humid environment, iron (Fe) will undergo an oxidation reaction: Fe→Fe²⁺ + 2e⁻. The generated electrons (e⁻) will be conducted through the metal, and Fe²⁺ will enter the electrolyte (such as soil and seawater containing water and dissolved salts). In another part of the metal surface, a reduction reaction will occur, for example, in the presence of oxygen, O₂ + 2H₂O + 4e⁻→4OH⁻. The continuation of this redox reaction causes the metal to dissolve continuously, that is, corrosion occurs.
The core idea of cathodic protection is to use external means to make the surface of the protected metal a cathode, thereby inhibiting the oxidation and dissolution process of the metal. There are two main ways to achieve cathodic protection: sacrificial anode cathodic protection method and impressed current cathodic protection method. They both rely on the anode to work.
In the sacrificial anode cathodic protection system, a metal or alloy with a more negative potential than the protected metal is selected as the anode. Since the potential of the anode material (magnesium, zinc, aluminum) is more negative, oxidation reaction will occur preferentially in the electrolyte solution, releasing electrons. These electrons flow to the protected metal, increasing the electron density on the surface of the protected metal, thereby inhibiting the corrosion reaction of the metal. For example, in a system where zinc is used as a sacrificial anode to protect a steel pipeline, zinc will continue to dissolve (Zn→Zn²⁺ + 2e⁻), while electrons flow to the steel pipeline, making it difficult to produce Fe²⁺ on the surface of the steel pipeline, thereby achieving the purpose of protecting the pipeline.
The impressed current cathodic protection system introduces direct current between the protected metal and the auxiliary anode through an external power supply. The auxiliary anode is usually made of highly corrosion-resistant materials, with the positive pole of the power supply connected to the auxiliary anode and the negative pole connected to the protected metal. The current flows out of the auxiliary anode and flows to the protected metal through the electrolyte solution, causing cathodic polarization on the surface of the protected metal and inhibiting the corrosion reaction. In this system, the auxiliary anode undertakes the key task of conducting current.
ICCP Anode VS Sacrificial Anode
The ICCP anode is suitable for the long-term protection of large, complex, or highly corrosive environments. It requires an external power source, but the current is controllable and the protection range is wide.The sacrificial anode is suitable for small, scattered, or hard-to-power scenarios. It does not require an external energy source, but the protection range is limited and the anode needs to be replaced regularly.The sacrificial anode is suitable for small, scattered, or hard-to-power scenarios. It does not require an external energy source, but the protection range is limited and the anode needs to be replaced regularly.
Comparison Items | ICCP Anode (Impressed Current Cathodic Protection Anode) | Sacrificial Anode |
Working Principle | Provide current through an external power source. The anode serves as an auxiliary electrode to release electrons, forcing the protected metal to become the cathode. | Rely on the corrosion and dissolution of its own metal to release electrons, making the protected metal become the cathode. |
Material Types | Mixed metal oxides (such as DSA), high-silicon cast iron, graphite, platinum/niobium coated titanium, etc. | Zinc-based, aluminum-based, magnesium-based alloys |
Driving Voltage | Dependent on an external power source (usually a rectifier), and the voltage is adjustable. | Dependent on the potential difference between two metals (natural corrosion potential difference), and the voltage is fixed. |
Current Output | Can be precisely controlled, with a large current intensity (usually several amperes to dozens of amperes). | The current output is limited by the corrosion rate of the material itself, and the current is relatively small (usually in milliamperes to several amperes). |
Protection Range | Suitable for long-distance and large-scale facilities (such as long-distance pipelines, large storage tanks). | Suitable for local or small-scale structures (such as ships, small pipelines). |
Maintenance Requirements | Regular inspection of the power source, anode status, and system parameters is required, and the maintenance is complex. | No external power source is required, but the consumed anode needs to be replaced regularly, and the maintenance is relatively simple. |
Service Life | The anode material has strong corrosion resistance and a long service life (usually 5-20 years, depending on the material and environment). | Dependent on the consumption rate of the anode material, and the service life is relatively short (usually 2-10 years). |
Environmental Adaptability | Applicable to high-resistivity environments (such as dry soil) or extreme corrosion environments (such as the deep sea). | Applicable to low-resistivity environments (such as seawater, wet soil). |
Cost | High initial investment (power supply equipment is required), but the long-term maintenance cost is low. | Low initial cost, but the anode needs to be replaced frequently, and the long-term cost may be high. |
Typical Applications | Oil and gas pipelines, bridges, port facilities, offshore platforms, large storage tanks | Ships, underground storage tanks, small pipelines, wharf facilities |
System Complexity | Requires supporting power sources, reference electrodes, and control systems, and the system is complex. | Simple structure, no external power source is required. |
Impact on Adjacent Metals | Stray current interference may occur, and additional protective measures are required. | There is no stray current problem, but it may accelerate the corrosion of adjacent low-potential metals. |
Environmental Friendliness | The anode material is usually environmentally friendly, but attention should be paid to the treatment of waste electrolyte. | The consumed anode material directly enters the environment and may have a slight impact on the local ecology. |
Factors in Selecting Anodes For Cathodic Protection
Correctly selecting cathodic protection anodes is of great significance to ensure long-term protection of metal structures, reduce maintenance costs, and ensure safe and stable operation of facilities. Selecting appropriate cathodic protection anodes is a complex and critical task, which requires comprehensive consideration of multiple factors such as the characteristics of the protected metal, electrolyte environment, protection current requirements, anode performance parameters, cost, and installation and maintenance. Different types of anodes have their own advantages and disadvantages in different application scenarios.
- Protected Metals
Different metals have different electrode potentials and corrosion characteristics, which directly affect the choice of anode. For metals with positive potential, such as copper and its alloys, anodes with more negative potential are required to provide sufficient driving voltage. For metals with more negative potential, such as steel, the range of anodes available is relatively wide, but factors such as corrosion rate and corrosion environment should also be considered.
- Soil Environment
The resistivity, pH value, water content and salts contained in the soil have a significant impact on the performance of the anode. In high resistivity soils, such as dry sandy soils, anodes with high driving voltage are required, and magnesium-based sacrificial anodes or impressed current anodes with high output capacity are more suitable. In low resistivity soils, zinc-based sacrificial anodes or ordinary impressed current anodes can meet the requirements. .
- Water Environment
In seawater, zinc-based and aluminum-based sacrificial anodes are common choices. They are stable in seawater. In fresh water, magnesium-based sacrificial anodes may be more suitable due to their high driving potential. For impressed current cathodic protection, mixed metal oxide anodes (MMO anodes) are more adaptable to the harsh environment of seawater due to their high oxygen evolution overpotential and long life.
- Current Efficiency
Current efficiency refers to the ratio of the effective protection current actually output by the anode to the theoretical output current. Anodes with high current efficiency use their own electricity more effectively and extend their service life. In seawater environments, the current efficiency of zinc-based sacrificial anodes can reach more than 80%.
- Life of Anodes
Mixed metal oxide anodes (MMO anodes) have a service life of up to decades due to their high oxygen evolution overpotential and good chemical stability. Although graphite anodes are less expensive, they may gradually wear out due to corrosion in certain environments and require regular inspection and replacement.
- Cost
Sacrificial anodes have a lower initial investment. Impressed current cathodic protection systems have a higher initial investment. For projects with limited budgets, sacrificial anodes may be more attractive. However, considering the long-term operating effect, impressed current cathodic protection systems may be more economical.
Custom Manufacturing Cathodic Protection Anode Services
Wstitanium provides high-quality and reliable solutions for various industries in the field of cathodic protection anode manufacturing with advanced technology, strict quality control and rich practical experience. From the selection of anode materials, optimization of manufacturing technology, to strict quality control system, Wstitanium is always committed to meeting your needs and solving metal corrosion problems in actual projects.
Sacrificial Anode
According to different sacrificial anode materials and specifications, appropriate casting technology is used. For zinc sacrificial anodes and aluminum sacrificial anodes, melting and casting technology is usually used. Pre-treated zinc ingots, aluminum ingots and other raw materials are added to the furnace in a certain proportion, heated and melted, and fully stirred during the melting process to make the alloy elements evenly distributed. Then the molten metal liquid is cast into a pre-made mold. The shape and size of the mold are determined according to the design requirements of the anode product. During the casting process, the casting temperature, speed and pressure are controlled to ensure the quality of the casting and avoid defects such as pores, shrinkage holes, and slag inclusions.
For magnesium sacrificial anodes, due to the active chemical properties of magnesium, special protective measures need to be taken during the casting process to prevent oxidation and combustion of magnesium liquid. Generally, melting and casting are carried out in a protective gas environment (such as argon), and an appropriate amount of refining agent is added to the magnesium liquid to remove impurities and gases and improve the quality of the casting.
High Silicon Cast Iron Anode and Graphite Anode
For high silicon cast iron anode, the casting process is used to process the high silicon cast iron billet into the required shape and size. During the casting process, the pouring temperature and cooling rate are strictly controlled to ensure the metallographic structure and performance of the high silicon cast iron. For graphite anode, according to the design requirements, the graphite block is processed into anodes of various shapes, such as cylindrical, plate, tubular, etc. by mechanical processing. During the processing, the dimensional accuracy and surface quality of the graphite anode are guaranteed to avoid defects such as cracks and falling blocks.
For mixed metal oxide anode (MMO), titanium is first mechanically machined to form the required shape, such as titanium rod, titanium tube, titanium mesh, etc., and then the active coating is coated on the surface of the titanium substrate by thermal decomposition or electrochemical deposition. The thermal decomposition method is to coat the surface of the titanium substrate with a solution containing metal salts such as ruthenium and iridium, and then thermally decompose it at high temperature after drying to convert the metal salt into metal oxide to form a firm coating. The electrochemical deposition method is to reduce and deposit metal ions on the surface of the titanium substrate through electrolysis to form a metal oxide coating.
Quality Inspection
Wstitanium strictly follows ISO 12959 “Sacrificial Anode Performance Requirements”, NACE RP0176 “External Corrosion Control of Underground or Underwater Metal Pipe Systems”, etc. to meet the needs of customers in different countries.
After the anode is manufactured, a comprehensive finished product inspection is carried out. For sacrificial anodes, its open circuit potential, closed circuit potential, current efficiency, consumption rate and other electrochemical performance indicators are tested. The constant current method or constant potential method is used to test in an electrolyte solution simulating actual working conditions. The potential and current changes of the anode are recorded by an electrochemical workstation to calculate various performance indicators. At the same time, the appearance, size, weight, etc. of the anode are checked to ensure that they meet product standards and customer requirements. For auxiliary anodes, in addition to testing their electrochemical properties, their conductivity, corrosion resistance, etc. are also tested. For example, high-silicon cast iron anodes are subjected to long-term corrosion tests to observe their corrosion in different media and evaluate their service life.
Cathodic Protection Anode Application
Whether it is the sacrificial anode that releases electrons by corroding and dissolving itself, or the auxiliary anode that transmits current under the action of an external power source, they play an irreplaceable role in their respective application scenarios. In the oil and gas industry, they ensure the safety and stability of energy transmission; in the field of shipbuilding and marine engineering, they extend the service life of offshore facilities; in municipal construction engineering, they ensure the long-term use of infrastructure.
Oil and Gas
In the oil and gas industry, cathodic protection anodes are widely used for corrosion protection of underground oil pipelines, natural gas pipelines, oil storage tanks, offshore oil platforms and other facilities. Underground oil pipelines and natural gas pipelines are buried in the soil for a long time and are easily corroded by factors such as electrolytes and microorganisms in the soil. Sacrificial anodes or auxiliary anodes are connected to the pipeline to form a cathodic protection system, which effectively inhibits the corrosion of the pipeline. The bottom plate and tank wall of the oil storage tank are in contact with the soil or the stored medium, and cathodic protection is also required to prevent corrosion. Offshore oil platforms are in a harsh marine environment, and the seawater is highly corrosive. The cathodic protection system is essential for the long-term safe operation of the platform’s steel structure, conductor frame, riser and other facilities.
Ship and Marine Engineering
The hull, propeller, rudder and other parts of the ship are immersed in seawater for a long time and face serious corrosion threats. Sacrificial anodes such as zinc-based sacrificial anodes and aluminum-based sacrificial anodes are widely installed on the surface of the hull to provide cathodic protection for the hull. For large ships and marine engineering equipment, such as drilling ships and floating production storage and offloading units (FPSO), impressed current cathodic protection systems are also used. Auxiliary anodes such as high-silicon cast iron anodes and MMO anodes are used in conjunction with sacrificial anodes to improve the protection effect. In addition, dock facilities such as piers and breakwaters often use cathodic protection technology to prevent corrosion from seawater and marine atmosphere.
Municipal and Construction Engineering
In municipal engineering, underground water supply pipes, drainage pipes, gas pipes and other infrastructure require cathodic protection to prevent soil corrosion. Bridges and building foundation steel bars in cities are also facing the risk of corrosion. By adopting cathodic protection technology, the service life of these structures can be extended. For some special buildings, such as swimming pools and sewage treatment pools, cathodic protection is also required to protect their structural safety because the contact medium is corrosive.
Power and Communication Industry
Metal facilities such as substation grounding grids and transmission line tower foundations in the power industry are exposed to soil or atmosphere for a long time and are susceptible to corrosion. Cathodic protection technology can effectively protect these facilities and improve the reliability of the power system. In the communications industry, underground communications cables, grounding systems of communications base stations, etc. also require cathodic protection to prevent corrosion and ensure smooth communications.
In summary, cathodic protection anodes play an important role in the field of metal corrosion protection. From a principle perspective, sacrificial anodes and auxiliary anodes build effective protective barriers for the protected metals based on different electrochemical mechanisms to resist corrosion. Sacrificial anodes such as zinc, aluminum, and magnesium, as well as auxiliary anodes such as high-silicon cast iron, graphite, and mixed metal oxides, each meet diverse engineering needs with their unique performance characteristics. The continuous improvement of Wstitanium’s manufacturing technology, from raw material inspection to quality control of the final product, ensures the high quality and reliability of the anode.