CNC Drilling Services
Wstitanium is able to manufacture components with intricate geometries and excellent surface finish to ensure the high quality standards our customers expect are maintained. Strict controls are applied at all stages of titanium part manufacturing, with a final inspection prior to dispatch.
- ISO 9001:2015, ISO 13485 Certified.
- Tolerances Up to ± 0.005mm
- 100% Quality Inspection Report
- Pay After Delivery
WSTITANIUM Factory
Our Powerful Facilities
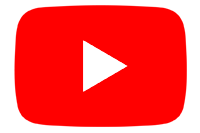
High-Quality CNC Drilling Services For Precision Titanium Parts
Wstitanium has an ongoing program of investment in the latest CNC machining centres, skilled, professional staff and systems. Our drilling centres are equipped with many drill options and multiple spindles, capable of manufacturing everything from deep precision drilled holes to components with intricate geometries and excellent surface finishes. Wstitanium is able to drill holes in both simple and complex patterns up to 102 mm in diameter. Tight control is maintained throughout the drilling process, ensuring that exacting tolerance standards are met every time. Advanced machines and a skilled team ensure high quality results for even the most detailed designs. A range of turnkey manufacturing services include boring, countersinking, drilling, reaming and tapping, among others.
What is CNC drilling?
CNC drilling is a computer-controlled subtractive manufacturing process where code guides a rotating drill bit to create a hole in a stationary workpiece to achieve accuracy and consistency that cannot be matched by manual operations. When drilling holes in metal, coolant is often used to reduce heat build-up, maintain accuracy, and extend tool life. When drilling deep holes with a CNC milling machine, pecking, or repeatedly passing the drill bit partially through the workpiece and then retracting it to the surface of the part, is often used because it helps remove chips. Precise and repeatable drilling operations to drill holes of varying depths, diameters, and shapes.
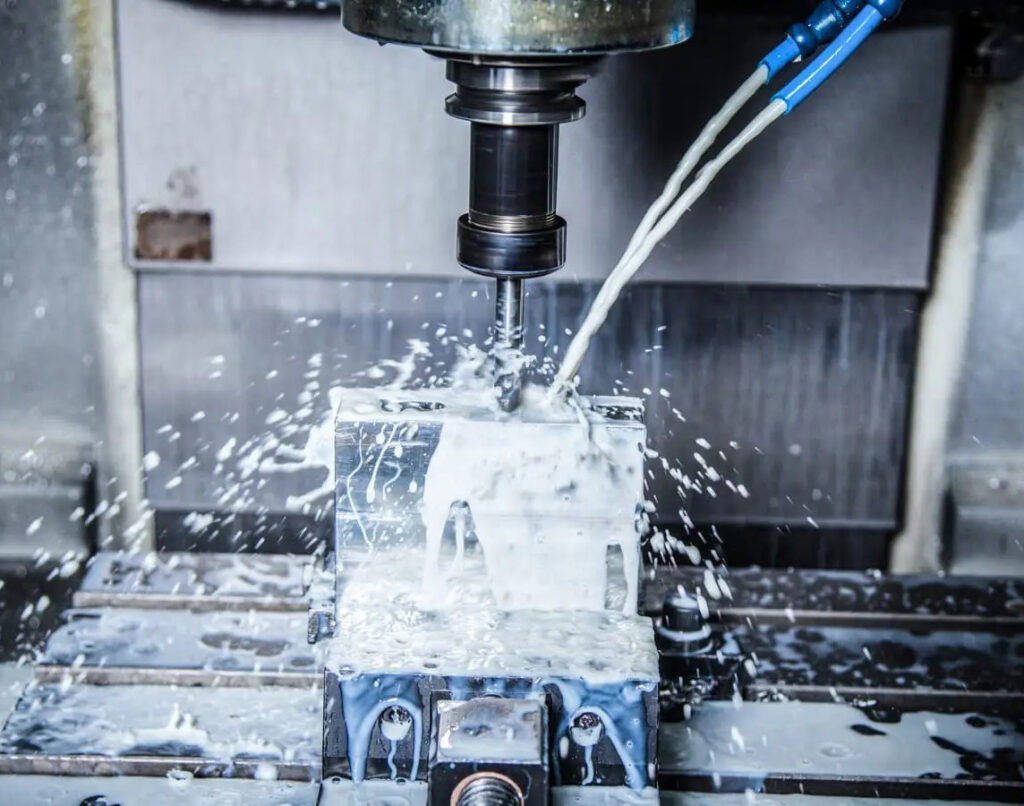
Holes are an essential feature of almost any part, whether for aesthetic or assembly purposes. In the precision-driven world of manufacturing, we need precise and accurate holes. This is where CNC drilling comes into play. This method is used in industries that require high precision, such as aerospace, automotive, and electronics. In these industries, even small differences can cause major problems.
How does CNC drilling work?
Compared to traditional drilling methods, CNC drilling significantly improves efficiency and productivity. This is mainly due to its automation, which minimizes human intervention and reduces the possibility of errors. The speed also exceeds that of manual processes, thereby reducing manufacturing time. It sounds like CNC drilling is just a simple operation. But it takes a lot of effort to achieve such precision. Here is the operation process of CNC drilling:
Step 1: Design and Planning
This stage creates the requirements for conceptualizing the product and planning the drilling, and translates them into digital designs. The workpiece geometry with all technical details and dimensions is designed on CAD software such as SolidWorks or Fusion 360. Including the location, size and depth of the hole, etc. CAD software is usually paired with CAM software to convert the design into G-code, a programming language understood by CNC drilling machines. At the same time, choosing the right material is also crucial to the success of the drilling operation. The material must not only be suitable for the intended use of the part, but also compatible with the drilling process.
Step 2: Choose the right drilling cycle
The G-code will guide the movement of the drill, the drilling speed, and the depth of each hole. Next, in the G-code programming, you can select any of the three drilling cycles based on your specific requirements:
G73 (chip breaking cycle): Suitable for holes deeper than three times the drill diameter, but within the effective length of the drill.
G81 (shallow hole circulation): Suitable for making center holes, chamfers, and holes that do not exceed 3 times the drill diameter. In addition, choose to drill with internal coolant to improve efficiency.
G83 (Deep Hole Circulation): For machining deep holes.
Step 3: Choose the right tool
The drill plays a key role in the process of creating a hole. Typically, a twist drill is used because of its versatility. However, center drills and step drills are also options for specific applications. Choosing a tool holder to hold the tool head is equally important. You need to consider the taper type, tool holder compatibility, etc. Common options for CNC drills are collet chucks, end mills, and hydraulic chucks.
Type of Drill Bit | Shape/Description | Application |
Twist Drill | Cylindrical shaft with a helical flute. | Versatile, for drilling in wood, walls, and a variety of materials. |
Center Drill | Short, rigid with a countersink and pilot section. | Creating starting points or ‘spots’ for precision drilling. |
Step Drill | Conical shape with stepped cutting edges. | Drilling holes of multiple diameters, especially in soft materials like aluminum. |
Ejector Drill | Tube-in-tube design with a carbide tip. | Making deep holes, ranging from 19-102 mm in diameter. |
Indexable Drill | Carbide or ceramic, wear-resistant with coolant channels. | Cutting large holes, about five times their diameter, efficiently. |
Step 4: Preparation before drilling
Before drilling begins, the machine needs to be set up. This includes mounting the drill, securing the workpiece, and calibrating the machine for accuracy. Position and clamp the workpiece securely on the machine. Make sure the tool drill is properly mounted in the tool holder. To secure the workpiece, use a retaining plate, clamp, or magnetic chuck. Place them close to the drilling area and do not overtighten them. Enter the necessary tool parameters, such as length and diameter, into the CAM system. These parameters are important to ensure that the tool will operate correctly within the predetermined specifications of the workpiece.
Step 5: The Actual Drilling Process
The drill follows the programmed path precisely. The drill moves to the specified coordinates and executes at the specified depth and diameter. The machine’s automated system manages speeds and feed rates, ensuring efficient and accurate drilling. Throughout the drilling process, continuous monitoring is essential to ensure that everything goes as planned. Adjustments may need to be made to account for any deviations.
Step 6: Quality Inspection and Surface Treatment
After drilling, check the accuracy and quality of the part. Technicians take measurements to ensure tolerances are within specified limits. Perform any necessary surface treatments, such as deburring or additional finishing, to meet final specifications.
Wstitanium CNC drilling capabilities
Wstitanium is a leader in custom, quick turnaround CNC machining and drilling services. We can handle almost anything regarding holes, but our area of expertise is efficient machining and drilling of tight tolerance shapes. This includes round, square, D-shaped, rectangular, flat oval, and other custom shapes.
EDM Drilling
- Discharge erodes the material to form a hole.
- Suitable for making small and complex holes.
- Widely used for drilling holes in hard metals.
Gun Drilling
- Produces precision holes with high aspect ratio.
- Facilitates coolant delivery and chip evacuation.
- Suitable for drilling deep and straight holes.
Gantry Drill
- The drill head moves along the gantry.
- Drilling is repeated many times on large parts.
- Suitable for drilling large plates. Such as ships.
Peck Drilling
- Break the drilling process into small increments
- Better chip evacuation and reduced heat build-up.
- Suitable for drilling holes in titanium parts.
Pillar Drilling
- Involves a vertical drilling machine.
- Suitable for creating holes with vertical precision.
- Suitable for repetitive drilling operations.
Spot Drilling
- Creates a small indentation or "spot".
- Ensures accurate drill bit positioning.
- Often used in precision machining operations.
CNC Drilling Experience Summary
A satisfactory CNC drilling service depends on the precise control of several key parameters. The setting of parameters determines the quality, efficiency and life of the drill and machine. Especially when CNC drilling titanium, its hardened surface and tangled chips can also cause serious damage to the quality and positioning accuracy of the workpiece. Maintaining quality will be more challenging when it comes to higher aspect ratios (the ratio of hole depth to diameter). Wstitanium summarizes the breakdown of the main parameters that are critical to CNC drilling titanium and how to measure them based on 15 years of CNC manufacturing experience.
Spindle speed (RPM)
Refers to the speed of the drill bit, measured in revolutions per minute (RPM). The optimal spindle speed varies depending on the material being drilled and the type of drill bit used. For example, harder titanium is drilled at a lower RPM to prevent overheating and drill bit wear.
Feed rate (mm/min or in/min)
The speed at which the drill bit enters the titanium, measured in mm/min or in/min. The correct feed rate depends on the drill size, material hardness and the desired hole quality. Feeding too fast can cause drill breakage, while feeding too slow can cause excessive wear.
Cutting Speed (SFM or m/min)
The speed of the cutting edge of the drill as it cuts titanium, measured in surface feet per minute (SFM) or meters per minute (m/min). Cutting speed is a function of spindle speed and drill diameter and is critical to tool life and surface finish. Due to the protective oxide layer on the surface of titanium alloys, drills can easily lose their sharpness and even run the risk of tool breakage. In addition to the tangled chips generated during the drilling process, not only is the quality of the workpiece at risk, but tool life will also be seriously unstable. The main challenge also lies in controlling the cutting (drilling) forces during the drilling process.
Depth of Cut
Indicates the depth of each drilling pass, especially in pecking operations. Adjust the depth of cut according to the characteristics of the titanium alloy and the type of drill to ensure efficient chip evacuation and minimize heat build-up. Wstitanium ultrasonic assisted machining technology provides superposition of tool rotation with longitudinal high-frequency oscillation, generating more than 20,000 micro-vibrations per second. This helps reduce cutting forces and promotes the chip evacuation process.
Tool material and geometry
Drill material (e.g., high-speed steel, carbide) and geometry (e.g., drill tip angle, groove design) are selected according to the drilling material and drilling conditions. These factors directly affect drilling performance, hole quality, and tool life.
Coolant and lubrication
The use of coolants or lubricants can reduce heat generation at the drilling site, improve chip evacuation, and extend the service life of the drill. The type and use of coolants or lubricants vary depending on the drilling material and drilling operation.
Applications of CNC Drilling
CNC drilling plays a vital role in modern manufacturing, providing greater precision and efficiency than manual processes. Its applications span a wide range of industries, each with unique requirements and challenges. Wherever parts need to be assembled, you need CNC drilling. Let’s explore how CNC drilling can be used in key areas.
| Examples |
The engine block, suspension mounts, wheel hubs | |
Fuselage parts, engine components, control panel casing | |
Electronics | Connector port, enclosure, circuit board housings |
Prosthetics, surgical instruments, dental implants | |
Industrial Machinery | Flange holes, machine frames, hydraulic components |
Energy Sector | Turbine hubs, pipeline flanges |
Consumer Products | Kitchen appliances, smartphone casing |
Start your CNC drilling project
Do you need custom CNC drilling services? Wstitanium will be your wise choice. We can make complex, close tolerance holes in a variety of titanium alloys. Commitment to quality ensures that every drilled component exceeds your expectations.
You know, Wstitanium’s expertise does not stop at CNC drilling, there is also a range of CNC machining services to meet all your precision manufacturing needs. Simply send your design drawings to [email protected] now. You will receive a quote within 3 hours and benefit from a free Design for Manufacturability (DFM) analysis provided by our skilled engineers. At Wstitanium, you will get a fast, simple and reliable solution to start your CNC drilling project today!