Finishing Services for Titanium
As a manufacturer specializing in titanium parts, Wstitanium deeply understands the importance of finishing services in tapping the performance potential of titanium materials and provides you with high-quality titanium product surface treatment solutions.
- ISO 9001:2015, ISO 13485 Certified.
- 100% Quality Inspection Report
- From Prototyping To Production
- From Production to Perfection
WSTITANIUM Factory
Our Powerful Facilities
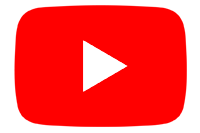
Customized Solutions For Titanium Finishing Services
Wstitanium has rich experience and advanced technology in the field of titanium surface treatment, including sandblasting, electroplating, anodizing, PVD, CVD, pickling, blueing, polishing, nitriding, micro-arc oxidation, etc., and can provide you with customized solutions. Each technique has its own unique principles, process parameters and application scenarios. Through strict quality control, we ensure that the titanium after finishing services have excellent performance and quality.
Sandblasting
Wstitanium uses compressed air as the power to spray abrasives (such as quartz sand, corundum, etc.) onto the surface of titanium products at high speed through a spray gun. The high-speed impact of the abrasive removes impurities, oxides, etc. on the titanium surface, and forms a microscopic rough structure on the surface. For general surface cleaning and roughening, quartz sand with a particle size of 80-120 mesh is commonly used; for situations requiring higher surface roughness and stronger impact effect, abrasives with higher hardness such as corundum will be selected, and the particle size can be between 40-80 mesh. The sandblasting pressure is usually controlled between 0.4-0.8MPa.
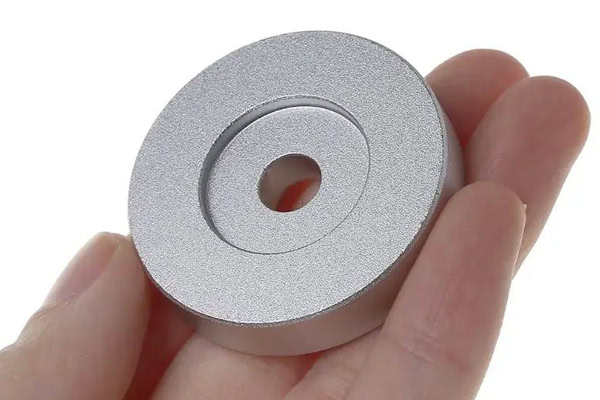
After sandblasting, the titanium surface becomes rough and uniform, and the roughness Ra value can reach between 1.6-6.3μm, which effectively enhances the bonding strength between the surface and subsequent coatings or other treatment layers. At the same time, sandblasting can also remove microscopic defects on the surface, improve the flatness and finish of the surface, and provide a good foundation for subsequent surface treatment.
Electroplating
Electroplating is the process of depositing a layer of metal or alloy on the surface of titanium using the principle of electrolysis. In the electroplating tank, the titanium product serves as the cathode, the metal to be plated serves as the anode, and the electrolyte contains ions of the metal to be plated. After power is applied, the metal atoms on the anode lose electrons and enter the electrolyte, while the metal ions in the electrolyte gain electrons at the cathode (titanium surface) and deposit to form a uniform metal coating. Wstitanium prepares electrolytes of different components. For example, when nickel is plated, the electrolyte mainly contains nickel sulfate, nickel chloride, boric acid and other components. Nickel sulfate provides nickel ions, nickel chloride enhances conductivity, and boric acid acts as a buffer to maintain the pH value of the electrolyte stable.
Electroplating can form a uniform and dense metal coating on the titanium surface, and the thickness can be controlled between 0.5 and 5μm according to demand. The coating can not only improve the corrosion resistance, wear resistance and conductivity of titanium products, but also give them decorative properties to meet the diverse needs of different customers.
Passivated titanium
Use chemical methods to form a dense oxide film on the titanium surface, namely the passivation film. Commonly used passivators include nitric acid, potassium dichromate and other solutions, which generate oxides such as TiO₂ on the titanium surface through chemical reactions. The titanium workpiece is immersed in the passivation solution, and the temperature is generally controlled at 20-50℃. The immersion time is 10-60 minutes depending on the concentration of the passivation solution and the requirements of the workpiece. Electrochemical passivation requires the control of parameters such as electrolyte composition, temperature, current density and passivation time. For example, in sulfuric acid-potassium dichromate electrolyte, the current density can be controlled at 0.5-2 A/dm², the temperature is 30-40℃, and the passivation time is 15-30 minutes.
Passivation can effectively isolate titanium from external corrosive media and significantly improve corrosion resistance. In chemical industry, marine engineering and other fields.
Anodizing
Titanium is used as an anode and placed in a specific electrolyte. Under the action of a DC electric field, an oxidation reaction occurs on its surface to form a porous oxide film. For example, in a sulfuric acid electrolyte, the anode reaction is Ti + 2H₂O – 4e⁻ = TiO₂ + 4H⁺, and the generated TiO₂ gradually accumulates to form an oxide film under the action of an electric field. There are various types of electrolytes, such as sulfuric acid, oxalic acid, phosphoric acid, etc. Taking sulfuric acid electrolyte as an example, the concentration is generally 15% – 25%, the temperature is 15 – 25℃, the voltage is 10 – 30 V, and the oxidation time is 20 – 60 minutes. By adjusting these parameters, the thickness, porosity and microstructure of the oxide film can be controlled.
Anodizing not only has good corrosion resistance, but also can obtain different colors by adjusting parameters, and has beautiful decoration. It is widely used in architectural decoration, electronic product casings and other fields.
Micro-arc oxidation
Based on ordinary anodizing, a layer of ceramic oxide film is grown in situ on the titanium surface by using micro-plasma discharge. When the voltage rises to a certain level, micro-plasma discharge will be generated in the electrolyte, and the instantaneous high temperature and high pressure will cause the oxide film on the titanium surface to melt and sinter, forming a ceramic film composed of oxides such as TiO₂. Involving parameters such as electrolyte composition, voltage, frequency, and duty cycle. The electrolyte usually contains components such as silicates and phosphates, with a voltage of 300-600 V, a frequency of 100-500 Hz, a duty cycle of 10%-30%, and a processing time of 10-30 minutes. Different parameter combinations can produce micro-arc oxidation films with different properties and structures.
Micro-arc oxidation has high hardness, good wear resistance, and strong corrosion resistance. In the fields of aerospace, automobiles, etc., it is used to improve the surface properties of titanium alloy parts and extend their service life. For example, the titanium alloy blades of aircraft engines can effectively resist gas erosion and corrosion after micro-arc oxidation treatment.
Physical Vapor Deposition (PVD)
The target compound is vaporized in a vacuum environment by physical methods (such as evaporation, sputtering, etc.), and then deposited on the surface of the titanium substrate to form a thin film. Evaporation coating is to heat the evaporation material to a high temperature to evaporate it. The evaporated atoms condense into a film on the surface of the titanium substrate; sputtering coating uses high-energy ions to bombard the target material, so that the target atoms are sputtered out and deposited on the titanium substrate. Evaporation coating requires control of parameters such as evaporation source temperature and evaporation rate. For example, the evaporation source temperature can reach 1500-2000℃, and the vacuum degree is maintained at 10⁻³-10⁻⁵ Pa. Sputtering coating requires adjustment of sputtering power, sputtering gas flow, target-substrate distance, etc. The sputtering power is generally 1-5 kW, the argon gas flow is 20-50 sccm, and the target-substrate distance is 5-10 cm.
PVD can deposit various functional films on the titanium surface. For example, titanium nitride (TiN) film has high hardness, wear resistance and good decorative properties, and is often used for tool coating and decorative surface treatment; titanium oxide (TiO₂) film has photocatalytic properties and can be used for self-cleaning surface preparation.
Chemical vapor deposition (CVD)
Use gaseous titanium compounds (such as titanium tetrachloride TiCl₄) and reaction gases (such as hydrogen H₂, nitrogen N₂, etc.) to react chemically under high temperature and catalyst to deposit a solid film on the surface of the titanium substrate. For example, TiCl₄ reacts with H₂ and N₂ at high temperature to form a TiN film, and the reaction formula is TiCl₄ + 2H₂ + N₂ = TiN + 4HCl. Involving parameters such as reaction temperature, gas flow rate, reaction time, etc. The reaction temperature is generally 800-1200℃, the gas flow rate is precisely controlled according to the reaction requirements, and the reaction time is 30-120 minutes. By adjusting these parameters, the growth rate, composition and structure of the film can be controlled.
CVD can produce high-quality functional films. The film has a strong bonding force with the titanium substrate and is suitable for occasions with high film performance requirements, such as the preparation of titanium metallization films in semiconductor manufacturing, and the surface protection of titanium alloy parts used in high temperature and high corrosion environments.
Pickling
Pickling is the process of using an acid solution to react chemically with oxides and impurities on the titanium surface to dissolve and remove them, thereby achieving the purpose of cleaning and activating the surface. Wstitanium Commonly used pickling solutions include mixed solutions of hydrofluoric acid, nitric acid, sulfuric acid, etc. Hydrofluoric acid can effectively dissolve the oxide film on the titanium surface, nitric acid plays an oxidation and auxiliary dissolution role, and sulfuric acid can adjust the acidity and conductivity of the solution. During the pickling process, the pickling solution reacts with the oxide film on the titanium surface as follows: TiO₂ + 6HF = H₂[TiF₆] + 2H₂O, dissolving and removing the oxide film.
After pickling, the impurities and oxide film on the titanium surface are completely removed, and the surface presents a metallic luster, achieving the purpose of cleaning and activation. The surface roughness after pickling is improved, which is conducive to the adhesion of subsequent coatings or treatment layers, while improving the corrosion resistance and appearance quality of titanium products.
Blue baking
Blue baking is the oxidation treatment of titanium in a solution containing an oxidant to form a blue or black oxide film on its surface. In Wstitanium’s blue baking process, alkaline solutions are usually used, such as solutions containing sodium hydroxide, sodium nitrite and other ingredients. Under heating conditions, the titanium surface reacts with the oxidant in the solution to form an oxide film mainly composed of trititanium tetraoxide (Ti₃O₄). The concentration of sodium hydroxide in the blue baking solution is generally between 50-100g/L, and the concentration of sodium nitrite is between 20-50g/L. The blue baking temperature is generally controlled between 130-150℃.
After blue baking, a layer of oxide film with a thickness of about 0.5-2μm is formed on the titanium surface, with uniform color and good decorative properties. At the same time, the oxide film can effectively isolate the titanium substrate from the external environment and improve its corrosion resistance and wear resistance.
Nitriding
Nitriding is the process of infiltrating nitrogen atoms into the titanium surface to form a nitrogen-rich hardened layer. Wstitanium mainly uses two methods: gas nitriding and ion nitriding. Gas nitriding is to place the titanium product in a sealed furnace containing nitrogen-containing gases such as ammonia at a certain temperature. The active nitrogen atoms produced by the decomposition of ammonia are absorbed by the titanium surface and diffuse inward to form a compound layer such as titanium nitride (TiN). Ion nitriding is to ionize the nitrogen-containing gas by glow discharge in a low vacuum environment. The nitrogen ions are accelerated to bombard the titanium surface under the action of the electric field, and the nitrogen atoms are injected into the titanium surface and diffused to form a nitriding layer.
After nitriding treatment, a nitriding layer with high hardness and good wear resistance is formed on the titanium surface, and the thickness is generally between 0.1-0.5mm. The hardness of the nitriding layer can reach 1500-2500HV, which significantly improves the wear resistance and service life of titanium products, while improving their corrosion resistance.
Conclusion
As a leader in titanium manufacturing, Wstitanium is fully aware of the huge potential of titanium and understands that surface treatment is the key to unlocking its full potential. Although the original surface state of titanium has certain basic properties, it is far from meeting today’s diversified and high-precision application requirements. Through appropriate surface treatment processes, such as nitriding and micro-arc oxidation, a very hard strengthening layer can be formed on the titanium surface. This makes titanium products more resistant to friction, wear and fatigue loads. In the high temperature, high pressure and high speed operation environment of aircraft engines, titanium alloy blades and gears that have been nitrided can operate stably for a long time, greatly improving the reliability and service life of the engine.