Mixed Metal Oxide Anodes Suppliers & Manufacturers In China
The mixed metal oxide anodes manufactured by Wstitanium are widely used in many important fields such as chlor-alkali industry, wastewater treatment, metal corrosion protection, electroplating, marine engineering, etc. due to their excellent performance.
- Iridium Coating
- Platinum Coating
- Ruthenium Coating
- Plate, Mesh, Tube, Customized
- For Electroplating
- For Sewage Treatment
- For Electrolysis of Water
- For Chlor-alkali Industry
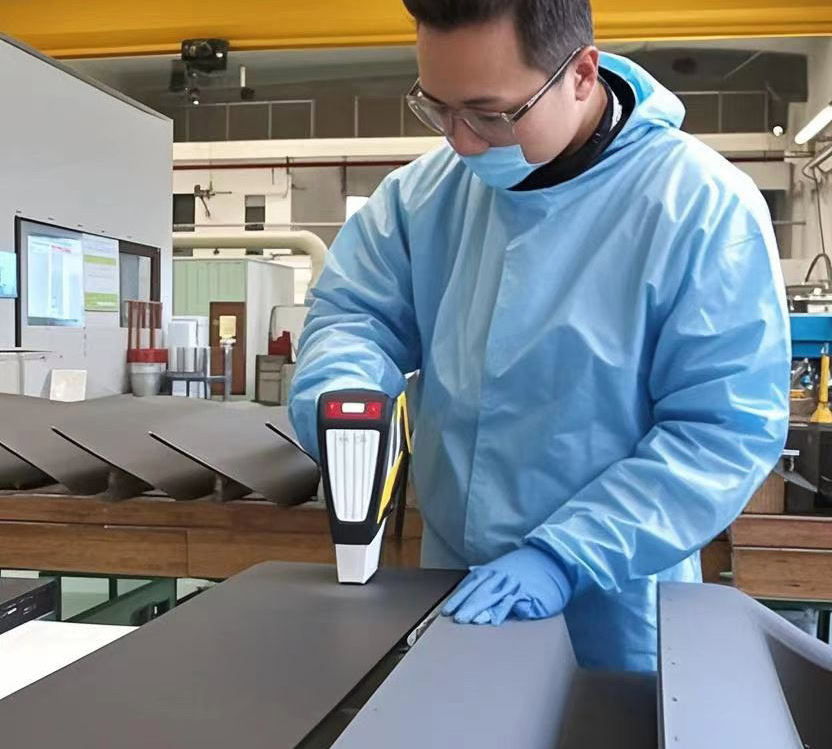
Your Trusted Supplier of Mixed Metal Oxide (MMO) Anodes
Mixed Metal Oxide (MMO) anodes play an indispensable role in many industries due to their outstanding properties, such as high catalytic activity, good stability and low resistance. Wstitanium has set an industry benchmark in the field of mixed metal oxide anode manufacturing with its superb technology, strict quality control and continuous innovation capabilities, and is your trusted partner and supplier.
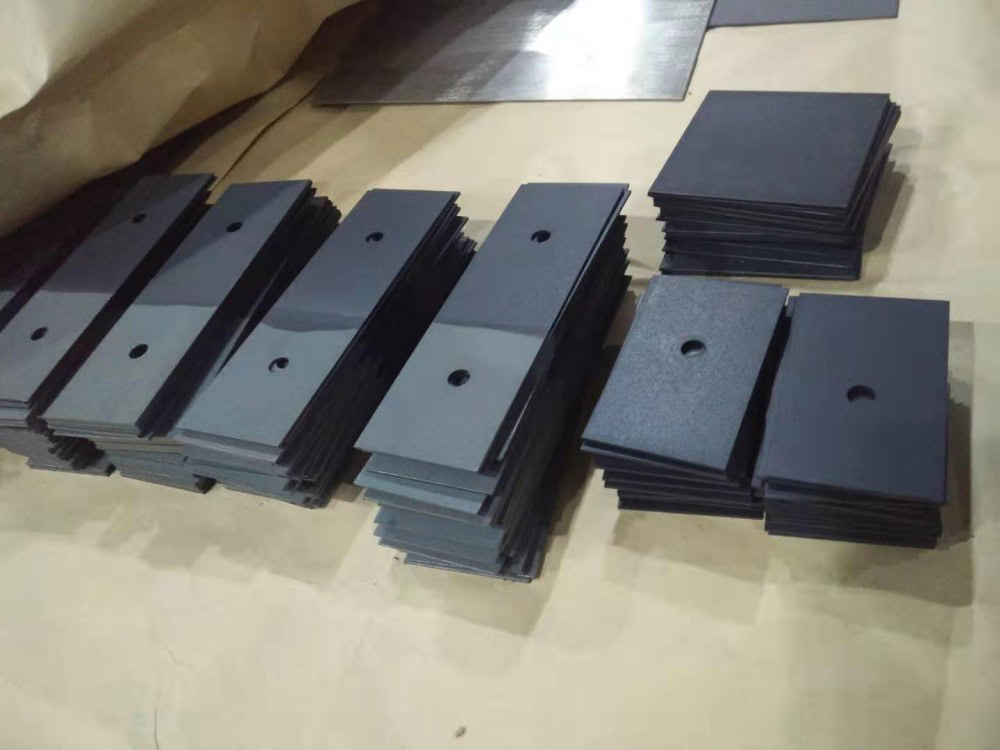
Using titanium (Ti) as the substrate, the active coating of ruthenium (Ru) oxide is coated. Ruthenium-based MMO anode has excellent catalytic activity for chlorine evolution reaction, making it one of the preferred anodes in the chlor-alkali industry.
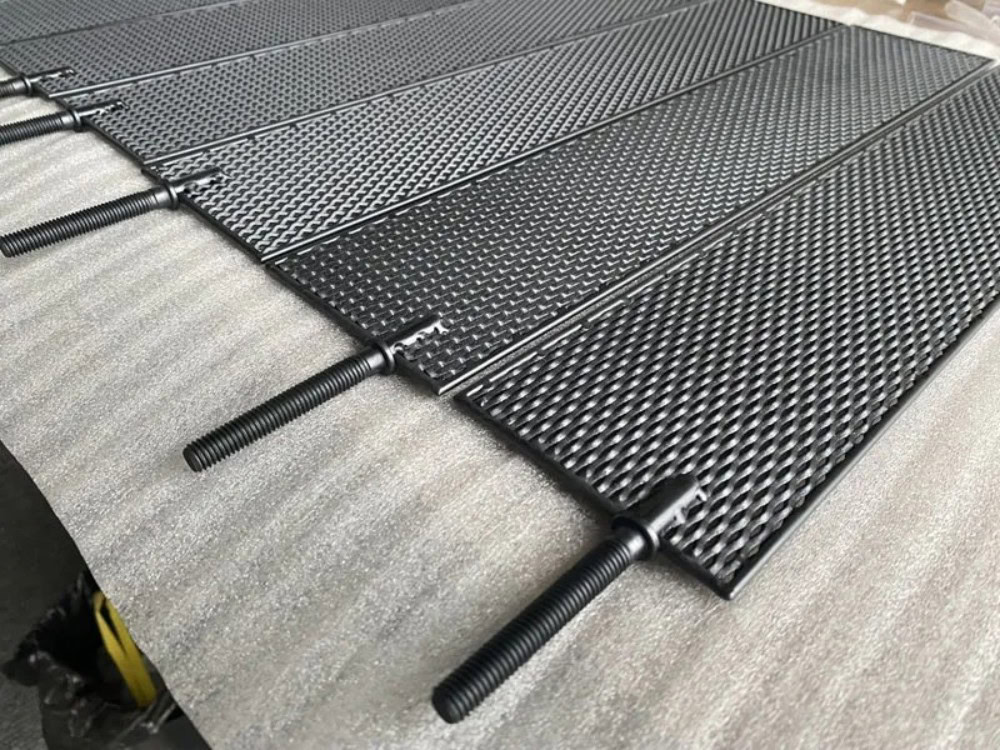
The titanium substrate is used, and the active coating mainly contains IrO₂. The iridium-based MMO anode exhibits excellent performance in oxygen evolution reaction, with low oxygen evolution overpotential and good stability.
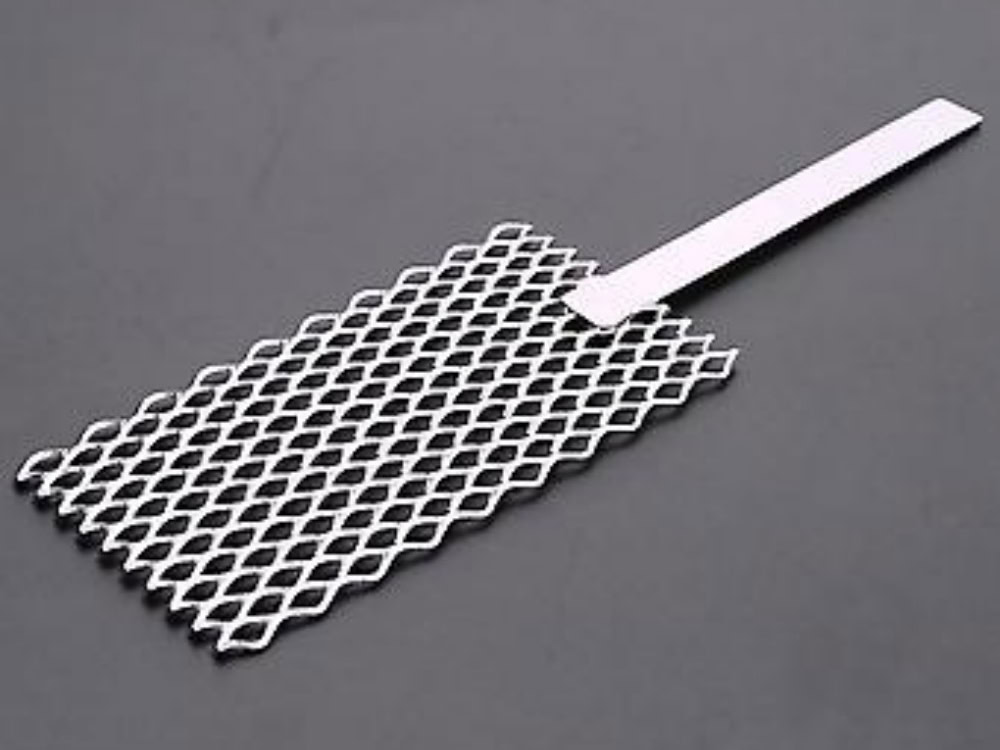
The titanium substrate is coated with a coating containing platinum (Pt) or platinum alloy (such as Pt-Ir alloy). It exhibits excellent catalytic performance for hydrogen evolution, oxygen evolution, oxidation of small organic molecules, etc.
Chlor-Alkali MMO Anode
The chlor-alkali industry MMO anode needs to have high chlorine evolution catalytic activity, low overpotential, good stability and long service life. It is usually a ruthenium or ruthenium-iridium composite coating to achieve chlorine gas precipitation with low energy consumption.
The MMO anode for wastewater treatment needs to have good electrocatalytic oxidation performance. The iridium-ruthenium composite MMO anode can make the color removal rate of wastewater reach more than 95% and the COD removal rate reach more than 80%.
Metal Anti-Corrosion MMO
MMO anode for metal anti-corrosion is mainly used in sacrificial anode cathodic protection and impressed current cathodic protection systems, with stable current output, high driving voltage and good corrosion resistance. Ruthenium or ruthenium-titanium composite coatings are often used.
Plate MMO Anode
Plate MMO anode is a flat plate structure with metal (such as titanium, tantalum) as the substrate and coated with metal oxide (such as RuO₂, IrO₂), providing a large effective surface area, suitable for scenes requiring uniform current density (such as electrolytic cells, metal electrodeposition).
Tubular MMO anode is a cylindrical structure formed by coating a metal oxide coating on the surface of a metal tube (such as a titanium tube). The symmetrical structure allows the current to be evenly dispersed in all directions, which is suitable for scenes requiring a three-dimensional current field.
Mesh MMO anode is a mesh structure formed by weaving or laser cutting metal wires and coated with metal oxides. The mesh structure significantly reduces weight and provides more active sites, which is suitable for scenes requiring efficient mass transfer (such as electrocatalytic degradation of pollutants).
How Do Mixed Metal Oxide Anodes Work?
The reason why the MMO anode has shown excellent performance in many fields is due to its unique working principle. It uses metals such as titanium and tantalum as the substrate, and the mixed metal oxide coating coated on its surface, such as RuO₂, IrO₂, etc., is the core functional layer of the MMO anode. These metal oxides can selectively catalyze specific redox reactions.
Electrolysis
During the electrolysis process, the MMO anode acts as an inert anode and does not participate in its own consumption. Instead, it catalyzes the oxidation reaction of anions (such as Cl⁻, OH⁻) in the electrolyte through the coating:
- Chlorine evolution reaction: 2Cl⁻ → Cl₂↑ + 2e⁻
(For chlor-alkali industry)
- Oxygen evolution reaction: 4OH⁻ → O₂↑ + 2H₂O + 4e⁻
(for water decomposition or sewage treatment)
Cathode Protection System
The MMO anode is the core component of the impressed current cathodic protection (ICCP) system. The anode conducts current into the electrolyte (soil, seawater or concrete pore fluid), making the protected metal (such as a pipeline) the cathode. The current released by the anode neutralizes the corrosion microbatteries on the metal surface and inhibits metal oxidation (Fe → Fe²⁺ + 2e⁻). Compared with magnesium alloy sacrificial anodes, the MMO anode has a 3-5 times longer life and an adjustable output current, which is suitable for long-distance linear projects (such as cross-regional oil pipelines).
Advantages of Mixed Metal Oxide (MMO) Anodes
MMO anode has demonstrated excellent performance in many electrochemical fields due to its many advantages such as high electrocatalytic activity, excellent corrosion resistance, long service life, low overpotential and good stability.
- High Electrocatalytic Activity
MMO anode is the key to improving electrocatalytic activity. Taking the chlorine evolution reaction in the chlor-alkali industry as an example, the chlorine evolution overpotential is 0.3-0.5V lower than that of graphite anode.
- Excellent Corrosion Resistance
MMO anode is based on titanium, tantalum and other substrates and has high corrosion resistance. The mixed metal oxide coating coated on its surface effectively resists the erosion of Cl⁻, O₂ and other substrates.
- Long Service Life
High electrocatalytic activity and excellent corrosion resistance work together to give MMO anode a long service life. The service life of MMO anode in the field of cathodic protection can reach 15-25 years (sacrificial anode 3-5 years).
- Low Overpotential
Overpotential is directly related to the energy consumption and efficiency of electrochemical reactions. In the oxygen evolution reaction of water electrolysis to produce hydrogen, the oxygen evolution overpotential of MMO anode is reduced by 0.2-0.3V compared with nickel-based anode.
- Good Stability
MMO anode maintains good stability under different working conditions. Its coating can work continuously at above 100℃. In electrolytes with different pH values, the passivation film can self-adjust to maintain protection of the substrate.
- Uniform Current Distribution
The structural design of the MMO anode allows for uniform current distribution during operation. Uniform current distribution helps improve reaction efficiency, ensure uniform product quality, and avoid local overheating or over-corrosion.
MMO Anode VS Graphite Anode
MMO anode is significantly superior to the other two in terms of electrocatalytic activity, corrosion resistance and life, and is suitable for high-demand industrial scenarios, but the initial cost is relatively high. The graphite anode has low cost but poor performance and is only suitable for low-demand or short-term applications. The nickel-based anode is stable in alkaline environments and has high hydrogen evolution efficiency, but has obvious disadvantages in oxygen evolution energy consumption and life.
Comparison | MMO Anode | Graphite Anode | Nickel – based Anode |
Material Composition | Titanium/tantalum substrate + mixed metal oxide coatings (such as RuO₂, IrO₂) | Graphite (carbon material) | Nickel or nickel – based alloys (such as Ni, Ni – Fe, Ni – Mo) |
Electrocatalytic Activity | Extremely high. Nanoscale active sites reduce the activation energy of reactions. The overpotential for chlorine evolution is 0.3 – 0.5V lower than that of graphite. | Relatively low. It relies on the electrical conductivity of graphite itself, and the overpotential is relatively high. | Moderate. The overpotential for oxygen evolution is 0.2 – 0.3V higher than that of MMO, and the overpotential for hydrogen evolution is about 0.1 – 0.3V. |
Overpotential (V) | Chlorine evolution: about 1.2 – 1.5V; Oxygen evolution: about 1.6 – 1.8V | Chlorine evolution: 1.5 – 2.0V; Oxygen evolution: 2.0 – 2.5V | Oxygen evolution: 1.8 – 2.1V; Hydrogen evolution: about 0.1 – 0.3V |
Corrosion Resistance | Excellent. The passivation film resists the erosion of Cl⁻ and O₂, and it can operate stably in strongly acidic/oxidizing environments. | Poor. It is easily corroded by Cl⁻ and rapidly consumed in acidic electrolytes. | Moderate. It has better corrosion resistance in alkaline environments, but it is prone to passivation or corrosion in acidic or Cl⁻ – containing solutions. |
Service Life | 15 – 25 years (cathodic protection) / 5 – 10 years (chlor – alkali industry) | 0.5 – 2 years (frequent replacement required) | 5 – 8 years (oxygen evolution scenarios) / 10 – 15 years (hydrogen evolution scenarios) |
Current Density (A/m²) | Can withstand high current density (5000 – 10000 A/m²) | Low current density (usually < 2000 A/m²) | Moderate current density (3000 – 6000 A/m²) |
Energy Consumption | Low. The low overpotential reduces power consumption, saving 20% – 30% of energy compared with graphite. | High. The high overpotential usually leads to high energy consumption. | Moderate. The energy consumption for oxygen evolution is relatively high, while that for hydrogen evolution is relatively low. |
Product Purity | High chlorine purity (> 99%), no carbon powder pollution | Chlorine contains carbon powder impurities, with relatively low purity (about 95% – 98%) | High oxygen evolution purity (> 99.5%), and hydrogen evolution contains a small amount of nickel ions. |
Maintenance Requirements | Low. The coating has strong self – healing properties, and regular inspection is sufficient. | High. Frequent replacement is required, and it is prone to fracture or peeling. | Moderate. It is necessary to prevent the dissolution of Ni²⁺ in alkaline solutions. |
Cost | High initial cost (complex coating process), low long – term comprehensive cost (low energy consumption + long service life) | Low initial cost, but high maintenance/replacement cost | Moderate initial cost, balanced life – cycle cost |
Application Scenarios | Chlor – alkali industry, sewage treatment, cathodic protection, electroplating, electrocatalytic synthesis | Aluminum electrolysis, low – requirement electrolysis (such as in laboratories) | Water electrolysis for hydrogen production (oxygen evolution), alkaline electrolyzers, nickel electroplating |
Environmental Impact | No heavy metal pollution, environmentally friendly | Generates CO₂ and carbon powder pollution | Limited nickel resources, and discarded anodes need to be recycled and processed. |
Structural Flexibility | Can be made into various forms such as plate – shaped, tubular, and mesh – shaped to adapt to complex scenarios | Relatively brittle, with a single structure |
MMO Anodes VS DSA Anodes
In the electrochemical world, especially in chlor-alkali manufacturing and wastewater treatment, the terms MMO (mixed metal oxide) and DSA (dimensionally stable anode) are often encountered. While there is commonality in the applications of the two, there are also differences between them. Notably, all MMO anodes qualify as DSA due to their structural integrity during the electrolysis process. However, DSA covers a broader category and is not limited to MMO coatings.
Comparison | MMO Anode | DSA Anode |
Definition | Mixed Metal Oxide anode. It is a metal electrode with industrial pure titanium as the substrate and covered with a thin film of precious metals and other metal oxides. | Dimensionally Stable Anode. It uses titanium as the substrate and has a thin and uniform layer of mixed metal oxides (MMOs) on its surface. |
Essence | Both belong to titanium – based metal oxide coated electrodes. MMO emphasizes the characteristics of mixed metal oxides. | DSA emphasizes the characteristic of dimensional stability. |
Coating Composition | Usually contains precious metal oxides such as RuO₂ and IrO₂, and may also have auxiliary components like TiO₂ and Ta₂O₅. | Similar to MMO, with platinum – group metal oxides as the main active components, such as ruthenium – based and iridium – based oxides. The ratio can be adjusted according to applications.Not limited to MMO coatings. |
Electrocatalytic Activity | High. Nanoscale active sites and special crystal structures effectively reduce the activation energy of reactions and promote electrochemical reactions. The overpotential for chlorine evolution is 0.3 – 0.5V lower than that of graphite. | High. It can significantly reduce the reaction overpotential and increase the reaction rate. For example, it can reduce the working voltage by more than 1 volt in the chlor – alkali process. |
Corrosion Resistance | Excellent. The dense passivation film formed in the electrolyte can resist the erosion of Cl⁻, O₂, etc., and is suitable for harsh environments such as strong acids and alkalis, and high – salt conditions. | Good. A protective oxide layer can form on the surface of the titanium substrate, with a “self – healing property” to maintain electrode performance in complex environments. |
Service Life | Long. It can reach 15 – 25 years (cathodic protection) and 5 – 10 years (chlor – alkali industry), depending on working conditions and coating quality. | Long. It can maintain stable operation for many years, greatly extending the service life compared with traditional carbon anodes and reducing the replacement frequency. |
Current Density | Can withstand a relatively high current density, generally reaching 5000 – 10000A/m², and some special designs can be even higher. | Can adapt to different current density requirements and meet the needs of various industrial electrolysis and electrochemical reactions. |
Operating Voltage | Low. The low overpotential enables electrochemical reactions to occur at a lower voltage, reducing energy consumption. | Low. It reduces the operating voltage in the electrochemical process and improves energy utilization efficiency. |
Application Fields | Widely used in chlor – alkali industry, sewage treatment, cathodic protection, electroplating, electrocatalytic synthesis and other fields. | Mainly used in chlor – alkali processes, the electronics manufacturing industry (such as copper foil electrodeposition, PCB, lithium – ion batteries), electrodeposition (copper, nickel, cobalt), surface treatment, electroplating, cathodic protection/corrosion prevention (traditional, concrete and seawater installations), and water treatment fields, etc. |
Manufacturing Cost | Relatively high. The preparation process is complex, involving titanium processing and high – precision coating application, and precious metal materials are used. | Relatively high. The processing of the titanium base and the process requirements for the mixed metal oxide coating are high. The cost mainly comes from raw materials and preparation technology. |
Weight | Light. Using titanium as the substrate, it is significantly lighter than traditional metal anodes, facilitating installation and operation. | Light. The characteristics of the titanium – based material determine its weight advantage, which is obvious in large – scale equipment. |
Maintenance Requirements | Relatively low. The coating has a certain self – healing ability, and regular inspection is sufficient. Abnormal situations such as scratching, short – circuiting, and overheating should be avoided. | Relatively low. The structure is stable, and maintenance work is minimal under normal operation. Attention should be paid to the impact of the operating environment on the electrodes. |
Environmental Impact | No heavy metal pollution, environmentally friendly. Some precious metals can be recycled after being scrapped. | No heavy metal pollution, environmentally friendly. Reasonable recycling and treatment can reduce resource waste. |
Structural Forms | Various forms such as plate – shaped, tubular, mesh – shaped, and strip – shaped, which can be customized according to different application scenarios and requirements. | Diverse. It can be made into various shapes and sizes to meet the needs of different industrial equipment and processes. |
MMO Anode Manufacturing
Thermal decomposition is one of the most classic methods for preparing MMO anodes. The principle is to apply a solution containing metal salts (such as metal chlorides, alkoxides, etc.) on the titanium surface, then decompose the metal salts by heating, and finally form a metal oxide coating on the substrate.
The specific process is as follows: First, the selected metal salt is dissolved in an appropriate organic solvent (such as ethanol, acetone, etc.) to form a uniform solution; then, the solution is applied to the surface of the titanium substrate that has been pretreated (such as polishing, acid etching, etc.) by dipping, spraying or brushing; then, the coated sample is dried at low temperature to remove the solvent; finally, the dried sample is placed in a high-temperature furnace, and the thermal decomposition temperature is usually between 400-600℃. The metal salt gradually decomposes into metal oxides and reacts chemically with the surface of the titanium substrate to form a strong bond.
The MMO anode prepared by thermal decomposition has the advantages of simple process, low cost, and easy large-scale production. The prepared anode coating has good adhesion to the substrate, which can ensure the stability of the anode in the electrochemical process to a certain extent. The MMO anode prepared by this method has been widely used in the chlor-alkali industry, general wastewater treatment and other fields with relatively conventional requirements for anode performance.
MMO Anode Application
MMO anode has been widely used in many fields such as chlor-alkali industry, sewage treatment, cathodic protection, electroplating, etc. due to its many advantages such as high electrocatalytic activity, excellent corrosion resistance, long service life, low overpotential and good stability, and has achieved significant economic and environmental benefits.
Chlor-alkali Industry
In the chlor-alkali industry, chlorine (Cl₂), hydrogen (H₂) and sodium hydroxide (NaOH) are mainly produced by electrolyzing salt water (NaCl solution). The MMO anode catalyzes the oxidation of chloride ions in this process. Its high electrocatalytic activity enables the chlorine evolution reaction to proceed efficiently, while the low overpotential reduces energy consumption. Compared with traditional graphite anodes, the low overpotential characteristics of the MMO anode can reduce the energy consumption of the electrolysis process by 15% – 20%. The MMO anode does not participate in chemical reactions and does not introduce impurities, so the purity of chlorine can reach more than 99.5%. In the highly acidic and oxidizing environment of the chlor-alkali industry, the excellent corrosion resistance of the MMO anode allows it to have a service life of 15-20 years, greatly reducing the number of anode replacements and downtime, and improving production efficiency.
Sewage Treatment
MMO anode is mainly used in processes such as electrocatalytic oxidation and electroflocculation in sewage treatment. The high electrocatalytic activity of MMO anode can promote the oxidation reaction of organic pollutants in water on the anode surface, decomposing them into harmless substances such as carbon dioxide and water. For some difficult-to-degrade organic pollutants, such as printing and dyeing wastewater, pharmaceutical wastewater, etc., the electrocatalytic oxidation of MMO anode can effectively remove the chemical oxygen demand (COD) and color in the wastewater, and improve the biodegradability of the wastewater. Studies have shown that when treating printing and dyeing wastewater, the COD removal rate can reach more than 70% when using MMO anode for electrocatalytic oxidation treatment.
Cathodic Protection
Cathode protection is to inhibit the corrosion of metal by applying cathodic current to the protected metal structure to reduce its potential below the corrosion potential. MMO anode acts as an auxiliary anode in the cathodic protection system to provide stable current output. MMO anode can accurately adjust the output current to meet the cathodic protection needs of metal structures of different sizes and shapes. In harsh environments such as soil and seawater, MMO anode does not need to be replaced frequently, which greatly improves the reliability and effectiveness of the cathodic protection system. MMO anode itself does not contain harmful substances and will not cause environmental pollution during operation.
Electroplating
During the electroplating process, the MMO anode can stably dissolve metal ions in the electroplating solution, providing a continuous metal source for electroplating, and its good conductivity and electrocatalytic activity can ensure the uniform distribution of current density during the electroplating process. The MMO anode can provide a stable current density, making the thickness of the electroplated layer uniform and the surface smooth, reducing plating defects caused by current fluctuations, such as pinholes and pitting. In copper plating, nickel plating, chrome plating and other processes, the use of MMO anodes can improve the quality and performance of the coating and enhance the bonding between the coating and the substrate.
With the continuous advancement of science and technology, MMO anodes have shown broad development prospects in the research and development of new coating materials, structural optimization and innovation, intelligence and multifunctionality, expansion of new application areas, integration with other technologies, and green and sustainable development. In the future, MMO anodes will continue to adapt to the needs of different fields, continuously improve performance, provide strong support for solving key problems in the fields of energy, environment, industrial production, etc., and promote technological progress and sustainable development in related industries.