Sheet Metal Assembly Services
Wstitanium provides custom fabricated components and sheet metal assembly services for a variety of industries, such as electrical and electronic enclosures, scientific equipment, and medical devices.
- Prototype to Low Volume Manufacturing
- ISO 9001:2015, ISO 13485 Certified.
- 100% Quality Inspection Report
- Parts as Fast as 1 days
- Global Delivery
WSTITANIUM Factory
Our Powerful Facilities
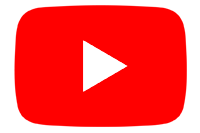
Sheet metal assembly titanium parts
Wstitanium provides electronic parts and custom sheet metal titanium assemblies for the world’s most advanced and important industries, including medical, aerospace, information and communications, renewable energy and entertainment. These titanium products are able to withstand the harshest environments and keep their good looks year after year. Wstitanium’s team of titanium sheet metal assembly experts use a variety of tools and techniques to achieve perfect functionality, structural integrity and dimensional accuracy while meeting strict quality standards. Ready to meet any challenge and help you speed up the time it takes to bring your titanium parts to market.
Titanium Sheet Metal Assembly
Sheet metal assembly is an essential part of precision manufacturing, where individual sheet metal titanium parts are meticulously joined together to create a final functional product. It involves a variety of techniques, including welding, fastening, and riveting, all of which are used to assemble custom assemblies with extreme precision. Sheet metal titanium component assembly is ideal for industries where precision is critical, such as automotive, aerospace, medical, and electronics, providing strong and seamless metal parts that can meet the needs of the intended application even in the harshest environments. Even the slightest deviation in the assembly process can result in a loss of product quality and performance, so Wstitanium’s assembly processes and assembly teams must ensure that each component fits together perfectly and performs its intended function with maximum efficiency and durability.
Common sheet metal assembly techniques
Regardless of size, sheet metal assembly presents its fair share of unique challenges that not every manufacturer is equipped to identify. Wstitanium knows how to help you avoid these challenges through specialized sheet metal technology. Various assembly techniques, including joint strength, accessibility, and throughput. So let’s discuss them in detail.
Fasteners
Wstitanium is fastened directly to sheet metal using fasteners such as nuts and screws. Fasteners can also be freely removed when changes are required. Fasteners such as screws and nuts will help you create non-permanent joints. This makes it easy to remove or replace parts without damaging them. Some of the types of fasteners used in sheet metal assembly include:
- Self-clinching nuts
- Self-clinching studs
- Counter-head studs
- Mini self-clinching nuts
- Round-head screws
- Flat-head pins
- Self-locking blind fasteners
- Sheet metal non-flush studs
- Self-clinching locking nuts
- Self-clinching miniature pins
- Self-locking counter-head nuts
- Round-head screws
- Square nuts
- Knurled nuts
- Barrel nuts
- Lock nuts
- Stud screws
- Frame screws
Sheet Metal Welding
Welding is the process of assembling metal parts using heat and pressure. When a strong and irreversible strong connection is required, Wstitanium uses welding sheet metal assemblies including manual welding and robotic welding. The most common welding capabilities include metal arc welding (MIG) and tungsten arc welding (TIG). The efficiency of these welding processes varies by speed, precision, and the quality of the joints they form.
- Avoid specifying welding methods.
- The materials must be consistent between parts.
- The minimum material thickness is 0.042 inches (1.07 mm).
- The maximum material thickness is 0.250 inches (6.35 mm).
- Always follow the welding positions specified on the drawing.
Robotic Welding
Welding robots perform certain welding activities together with welding guns. It can maintain the uniformity and accuracy of the welded product, thus providing reliable output, and compared with manually operated welding processes, it can also reduce labor costs and keep the weld size uniform and determined. But it requires a large investment and is difficult to adapt to too complex tasks.
Manual Welding
Manual welding is superior in flexibility and accuracy because the operator can easily implement different welding working conditions for different material thicknesses and joint types. Therefore, the welder’s operating accuracy is high. However, it requires higher skills from the welder and takes longer to weld.
Sheet Metal Rivet Assembly
If you are looking for extra flexibility when joining metal parts, you can consider riveting. Riveting is a technique for joining parts together using hardware. Rivet assembly is suitable for joining parts that experience pressure and temperature changes or for joining parts that are structurally strong. There are many types of rivets used in sheet metal assembly, such as:
- Solid rivets: Join parts with a visible head on one end and a headless end.
- Blind rivets: They are usually inserted into holes made to join parts.
- Pulled rivets: Add structural rigidity to the joined sheet metal parts.
- Threaded rivets: Used for parts used in high-performance applications.
- Drive pin rivets: Used in construction or to enhance the aesthetics of a part.
- Tubular rivets: These rivets are hollow and come in different structures.
Adhesives
Bonded assembly is the process of attaching sheet metal components using adhesives. This technique does not require the use of fasteners or welding methods. Here is how it works:
- Surface preparation: Cleaning the surfaces of the sheet metal components to be bonded.
- Adhesive application: Placing the adhesive or bonding agent on the components.
- Strong connections: Most provide a secure and reliable grip.
- Versatility: Can be used on many different materials.
- Structural adhesives: Enhance the heat, chemical, and temperature resistance of parts.
- Anaerobic adhesives: Think of them as threadlockers and pipe sealants
- Cyanoacrylate adhesives: Resistant to impact and polar solvents.
- UV-curing adhesives: Suitable for assembling metal hinges, fixtures, and knobs.
- MS polymer adhesives: Provide excellent aesthetic results.
Sheet metal hinge assembly
Sheet metal hinges are hinges that are bolted or welded to two sheet metal parts and designed to rotate around a central axis, allowing movement between the two parts. The most common type of hinge opens and closes doors or lids, just like hinges on cabinets and boxes. Hinges can be made of steel, aluminum, and titanium. The choice of metal depends largely on the application. Aluminum is lighter but not as strong as stainless steel or titanium, but since it does not rust, it is a good option for products that will get wet or be placed in wet locations.
- Hinge Installation: Prepare and mark the two connecting edges on the corresponding positions of the sheet metal parts.
- Fastening Operation: Screws or rivets are used to fasten hinges or other structures made of sheet metal.
- Hinge Function: Hinge allows parts to swing or rotate in a frictionless manner.
Of course, sheet metal assembly also includes rivet assembly, brazing assembly, tongue and groove assembly, snap fit, snap fit, mortise and tenon joints. It focuses on the technology of sheet metal assembly connection. Sheet metal assembly plays a role in the pursuit of growth and competitiveness. It provides versatility and flexibility. Want to assemble your titanium sheet metal parts, please get a quote from Wstitanium.
Common sheet metal assembly products
Sheet metal assembly products are everywhere, supporting and enriching the modern manufacturing industry. From the grand aerospace field to small and exquisite daily products. Sheet metal assembly demonstrates its indispensable value with its unique performance and diverse uses.
– Aircraft engine parts: casings, oil leak boxes, heat shields, etc., using isothermal hot forming technology to achieve integrated forming of complex thin-walled components of titanium alloy.
– Titanium-steel composite plate equipment: such as the tube sheet of the condenser used in power generation equipment, which is composed of titanium plate and steel plate.
– Sheet metal shell: The shell of some high-end equipment is made of titanium alloy sheet metal, which uses its high strength-to-weight ratio and corrosion resistance to maintain excellent performance in extreme environments.
– Bicycle frame: Titanium bicycle frame, which is assembled by high-precision laser cutting of titanium plates, welding, grinding, surface treatment and other processes.
Quality Inspection
Quality inspection is an important stage in the metal assembly process. These inspections include dimensions, surface finish, straightness, flatness, concentricity, perpendicularity, contours and other structures. To check and control quality, it is important to use a variety of tools
Dimensional Accuracy: It ensures that the sheet metal parts meet the expected dimensions. Of course, they are within the preset tolerance limits. Calipers and micrometers are used to measure geometric dimensions. On the other hand, coordinate measuring machines and gauges are used for dimensional inspection.
Surface Finish: This helps to confirm that the sheet metal parts have the right surface finish and are free of defects, i.e. cracks, marks, indentations or rust. Surface roughness and surface morphology are measured and evaluated by visual inspection and surface profilometers respectively.
Structural Integrity: Nondestructive testing is performed regularly to look for possible damages such as cracks, weld discontinuities or material defects that affect the entire assembly. Ultrasonic testing and magnetic particle testing help to check for defects hidden in the respective materials without causing any damage to the material.
CMM: CMM is a precision instrument used to check and verify the dimensional and geometrical properties of various sheet metal parts. Hence, they can conform to the design and standards set at the time of initial design. Standard machines with fixed gantry and feed table are suitable for medium to large workpiece sizes.
Ultrasonic Inspection: This method also works by directing high-frequency sound waves onto the object. Hence, it analyzes the reflected sound waves to determine the defects within the object.
Optical Inspection Systems: Optical inspection systems use cameras and sensors to visually inspect surface finish, weld coating joints, and assembly tolerances.