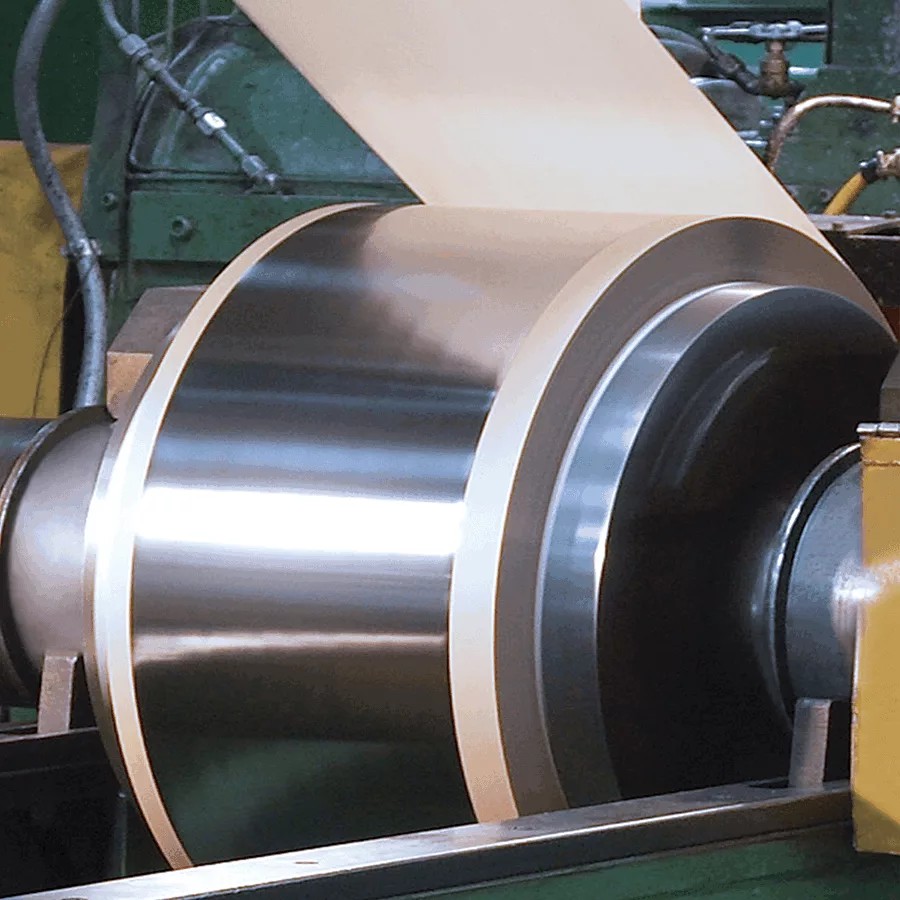
Titanium Foil With Competitive Price In China
Wstitanium is your trusted partner in the field of titanium foil manufacturing with its continuous technological innovation, strict quality control and in-depth understanding of your needs. It covers pure titanium and various titanium grades, and has shown great application value in many fields such as aerospace, electronic information, medical equipment, energy, chemical industry and marine engineering.
- Gr.1
- Gr.2
- Gr.3
- Gr.4
- Gr.5
- Gr.7
- Gr.9
- Gr.10
- Gr.11
- Gr.12
- Gr.16
- Gr.17
- Gr.23
- Gr.27
- Gr.29
- GB/T3621.ASTM B265
- Thickness: 0.002-3.0 mm
- Tolerance: up to ±0.002 mm
- Supply capacity: 300 tons per month
- Customization available upon request
Your Resource of Titanium Foil Manufacturers & Suppliers - Wstitanium
Titanium foil has attracted much attention due to its unique combination of properties. From aerospace to electronic devices, from innovative designs of medical devices to emerging solutions in the energy field, titanium foil plays an indispensable role. As a leader in titanium foil manufacturing, Wstitanium is committed to providing high-quality, customized titanium foil to customers around the world with its advanced technology, strict quality control and unremitting pursuit of innovation. Next, let us learn about the information of Wstitanium manufacturing titanium foil, including titanium grades, types, manufacturing technology, quality inspection, applications, etc., aiming to provide you with a comprehensive and in-depth reference.
- Length: ≥6000mm
- Width: 50mm-200mm
- Technique: Cold Rolled
- Thickness: 0.02mm-0.09mm
- Standard: ASTM B265/ASME SB265
- MOQ: 1kg
- Leading Time : 3-20 Days
- Package : Plywood Boxes
- Form : Single Strip, Coiled Oron Spool
- Shipment : DHL, UPS, FEDEX / By air / By sea
Gr1 Titanium Foil
Gr1 titanium foil performs well in applications with high corrosion resistance, such as some container linings and decorative materials in the food and chemical industries. Its tensile strength is generally between 240 and 345MPa.
Gr2 Titanium Foil
Compared to Gr1, Gr2 titanium foil has slightly higher strength. It is one of the most widely used pure titanium grades. For example, in shipbuilding, it can be used for seawater contact parts. Its tensile strength is between 345 and 450MPa.
Gr5 Titanium Foil
This is one of the most commonly used α+β type titanium alloys. It has high strength, stress resistance, crack toughness, high temperature performance, and excellent corrosion resistance in most industries. For example, marine, chemical, etc.
Ultra - Thin Titanium Foil
It has extremely high flexibility and lightweight characteristics. It is widely used in the electronics field, such as flexible circuit boards, electronic shielding materials, etc.
Conventional - Thickness Titanium Foil
Thickness is 0.02-0.1mm. It has a good balance between strength, flexibility and machining performance. It is used in medical packaging, anti-corrosion coatings, etc.
Thick Titanium Foil
Thickness is greater than 0.1mm. It has high strength and rigidity and is often used in applications that need to withstand large pressures or loads, such as sealing materials.
Smooth Surface Titanium Foil
The surface is finely rolled and polished, with extremely high surface finish, in the range of Ra0.1 – Ra0.5μm. It is used for the appearance decoration of optical instruments and high-end electronic products.
Matte Surface Titanium Foil
Through special surface treatment technology, the surface of the titanium foil presents a uniform matte texture. Commonly used in the housing of handheld electronic devices, tool handles, etc.
Coated Titanium Foil
One or more functional coatings are applied to the surface of the titanium foil to give the titanium foil additional properties. Such as anti-corrosion coating, insulation coating, wear-resistant coating, etc.
The performance of titanium foil depends largely on its titanium grade. Different grades correspond to different chemical compositions and mechanical properties, and are suitable for different application scenarios. Wstitanium provides a variety of grades of titanium foil to meet different needs.
Custom Manufacturing Titanium Foil
Wstitanium’s advanced and complete titanium foil manufacturing process, from the selection of raw materials to the final product, every link is carefully designed and strictly controlled to ensure high quality and consistency.
Raw Materials
High-quality titanium ingots are the basis for manufacturing titanium foil. Industrial pure titanium ingots (>99.9%) and titanium alloy ingots are selected according to different requirements, and their purity, composition uniformity and other indicators should be paid attention to. According to the design requirements of titanium foil, some alloy elements such as aluminum, vanadium, molybdenum, etc. are added to improve the strength, toughness, corrosion resistance and other properties of titanium. The ingot is heated to 800-1000℃ to improve the plasticity of titanium, reduce deformation resistance, and facilitate subsequent rolling. The heated ingot is surface treated to remove impurities such as oxide scale and oil stains on the surface. Common methods include mechanical grinding and pickling to ensure good contact between the roller and the billet surface during rolling.
Rolling is to apply pressure to the titanium billet through rotating rollers to make it plastically deform, so as to achieve the purpose of reducing thickness, changing shape and improving performance. In the manufacture of titanium foil, multi-pass rolling is usually adopted. Rolling equipment includes rolling mills, coilers, uncoilers, etc. There are many types of rolling mills, such as two-roll mills, four-roll mills, multi-roll mills, etc. For titanium foil rolling, high-precision multi-roll mills are often used to ensure rolling accuracy and plate shape control.
Rough rolling
Rough rolling is generally divided into 3-5 passes, and the amount of each pass is relatively large, which can reduce the billet thickness from tens of millimeters of ingots to several millimeters. The rough rolling speed is usually controlled at 0.5-1.5m/s to avoid cracking due to excessive rolling force.
Intermediate annealing
There is residual stress inside the titanium foil billet after rough rolling, and the structure is uneven. Intermediate annealing can eliminate residual stress, refine grains, improve plasticity and toughness, and prepare for subsequent finishing rolling. The annealing temperature is generally between 600-800℃, and the holding time is usually 1-3 hours. The annealing atmosphere is usually protected by vacuum or inert gas to prevent oxidation of the titanium foil surface.
Finishing rolling
Finishing rolling is the key link to obtain high-quality titanium foil, using smaller reduction and higher rolling accuracy. The reduction is usually controlled between 0.01-0.1mm to achieve the target thickness and surface quality. By adjusting the parameters such as the convexity of the roller, the bending force and the rolling tension, the plate shape of the titanium foil is accurately controlled to meet the requirements of flatness and thickness uniformity.
Post-rolling Treatment
The surface of the titanium foil after cold rolling will have residual rolling oil and other impurities, which need to be cleaned. Use special cleaning agents and cleaning equipment to remove surface oil and impurities by spraying, soaking, etc. Annealing is used to eliminate residual internal stress, stabilize the organizational structure of the titanium foil, and improve its mechanical properties and corrosion resistance. The annealing temperature and holding time are adjusted according to the alloy composition of the titanium foil and product requirements. Generally, the annealing temperature is 500-700℃, and the holding time is 1-3 hours. After annealing, the titanium foil is cooled with the furnace or quickly cooled to room temperature. Polishing, grinding, etc. further improve the surface finish and reduce the surface roughness.
Quality Inspection
Generally, the thickness tolerance of titanium foil is relatively high, such as ±0.005mm or less. The tensile strength, yield strength, elongation and other mechanical properties of titanium foil are measured by tensile test to ensure that they meet the corresponding design requirements. At the same time, hardness test is carried out to check whether the hardness of titanium foil is uniform. The surface roughness Ra value reaches 0.1 – 0.5μm or less. The organizational structure of titanium foil is analyzed by metallographic microscope, X-ray diffractometer and other equipment to check whether the grain size, phase composition, etc. meet the requirements. Uniform and fine grain structure helps to optimize the mechanical properties of titanium foil.
Titanium foil manufacturing is a complex system engineering. Rolling is the core link. By strictly controlling the quality of raw materials, optimizing smelting and ingot casting, accurately grasping rolling parameters, and doing a good job of surface treatment and quality inspection, Wstitanium produces high-quality titanium foil to meet the application needs of different fields.