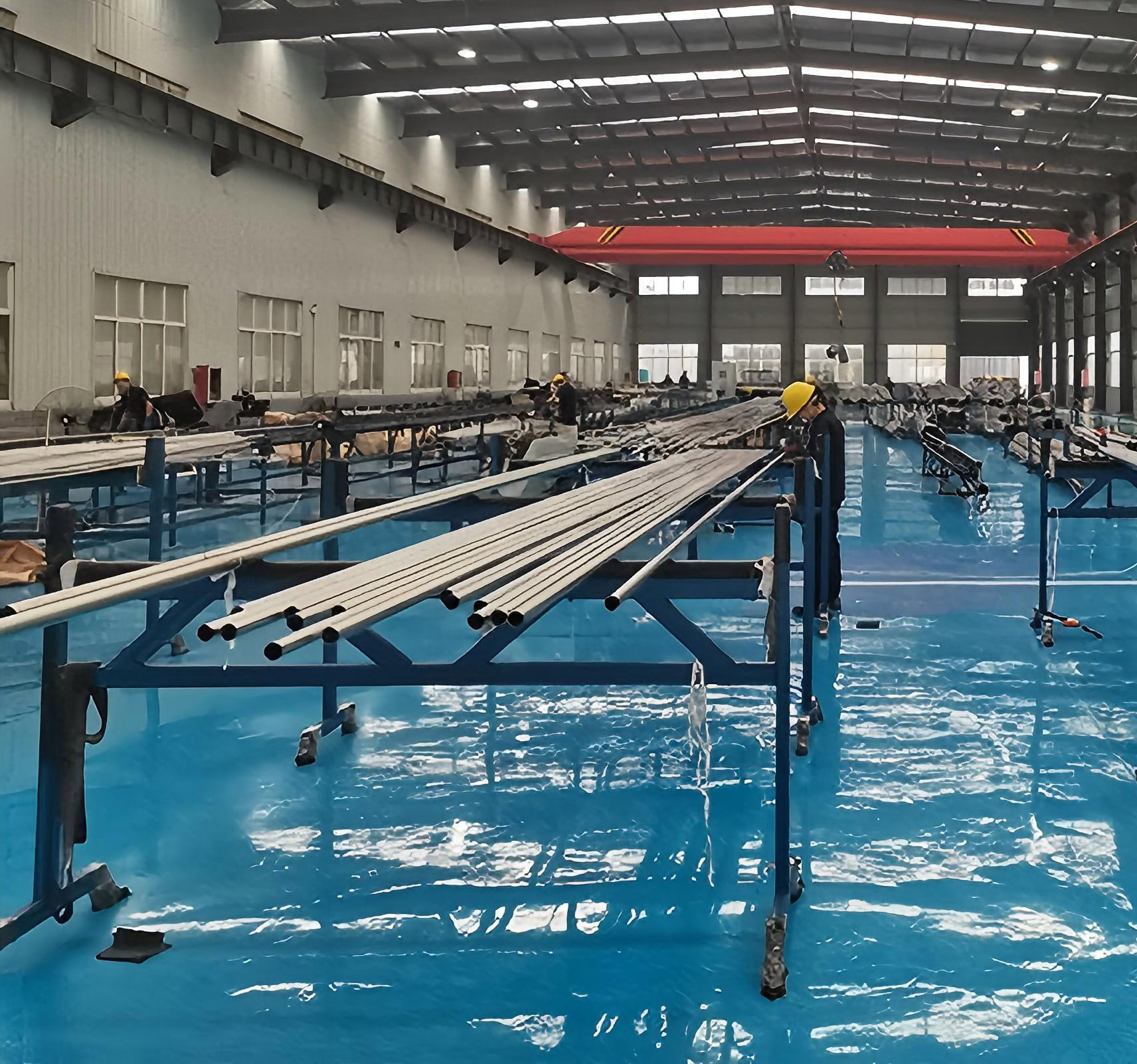
Titanium Tubes & Pipes With Competitive Prices
Wstitanium’s outstanding performance in the field of titanium tube manufacturing is not only reflected in its advanced technology, strict quality control and a wide range of types and applications, but also in its deep insight into and active promotion of the development of the titanium industry.
- Gr.1
- Gr.2
- Gr.3
- Gr.4
- Gr.5
- Gr.7
- Gr.9
- Gr.10
- Gr.11
- Gr.12
- Gr.16
- Gr.17
- Gr.23
- Gr.27
- Gr.29
- Form: Round, Hydraulic Etc
- Surface: Pickled or Polished
- Vickers Hardness:830–3420 MPa
- Customization available upon request
- End: Plain End, Beveled End, Threaded
A Trusted Titanium Tube & Pipe Manufacturer and Supplier -Wstitanium
Titanium tubes are gradually emerging in more fields due to their unique properties such as excellent corrosion resistance and good biocompatibility. Titanium tubes remain stable in harsh environments such as strong acids and alkalis. For example, in the chlor-alkali industry, titanium tubes are used to transport highly corrosive substances such as chlorine and sodium hydroxide. In the field of petrochemicals, titanium tubes provide solid protection in pipeline systems such as reactors, heat exchangers, and distillation towers, whether in high-temperature and high-pressure environments or in the transportation of materials containing various impurities and corrosive components.
Titanium Seamless Pipe
Seamless titanium tube has high strength and strong corrosion resistance, and is used in aerospace, chemical industry, medical treatment, etc.
- Outer Diameter Range: 0.4 – 340 mm
- Wall Height Range: 0.4 – 10 mm
- Length Range: < 18000 mm
Titanium Welded Pipe
It is necessary to work under the protection of inert gas, strictly control welding parameters, and ensure the quality of welds.
- Outer Diameter Range: 90 – 5,000 mm
- Wall Height Range: 0.5mm – 50mm
- Length Range: < 15000 mm
Customized Titanium Tubes
Customized titanium tubes precisely match specifications and performance. Strict quality inspection ensures compliance with standards.
- Standards: ASTM DIN AMS
- Material: CP Grades 1 – 4
- Alloys: Grade 5, 7, 9, 10, 12, 24, 26, 29 etc
Pure Titanium Tube
Pure titanium tubes are made of high-purity titanium (Gr1, Gr2, Gr3, Gr4), with low density and excellent corrosion resistance.
Titanium Alloy Tube
Titanium alloy tubes are made of titanium with other elements (aluminum, manganese, molybdenum, etc.) added to them. They are divided into α, β, and α+β.
Medical Titanium Tube
Excellent biocompatibility greatly reduces the risk of rejection. For example, bone plates, artificial joints, heart stents, etc.
Square Titanium Tubes
Its unique square cross-section plays a key role in aerospace, architectural decoration, chemical equipment manufacturing and other fields.
Round Titanium Tubes
The round structure is evenly stressed and can better withstand internal and external pressure. Round titanium tube is the most popular style.
Capillary Titanium Tube
The tube diameter is extremely fine and is used for transporting trace amounts of liquids in precision instruments, chemicals, aerospace, etc.
Titanium Tube Manufacturing
Sponge titanium is the main raw material for manufacturing titanium tubes, and its quality directly affects the performance of titanium tubes. Wstitanium strictly inspects the chemical composition, purity, and particle size of sponge titanium in accordance with relevant standards. For titanium alloy tubes, various alloy elements need to be accurately added according to different grades and performance requirements. Wstitanium’s advanced batching system can accurately control the amount of alloy elements added to ensure the uniformity and stability of the alloy composition. For example, when making GR5 (Ti-6Al-4V) titanium alloy tubes, aluminum and vanadium elements are added in a strict ratio of about 6% and about 4%, and are evenly distributed in the titanium matrix through stirring, smelting, etc.
The electrodes made of titanium sponge and added alloying elements (if it is a titanium alloy tube) are placed in a vacuum consumable arc furnace for melting. In a vacuum environment, the electrode is gradually melted and dripped into the crucible through the arc generated between the electrode and the water-cooled copper crucible to form titanium liquid. Due to the cooling effect of the water-cooled copper crucible, the titanium liquid quickly solidifies to form an ingot. During the melting process, gas impurities such as hydrogen, oxygen, and nitrogen are extracted.
In order to further improve the quality and performance of the ingot, secondary melting may be required for some titanium tubes for high-end applications. Secondary melting usually adopts electron beam cold hearth furnace melting (EBCHM). Electron beam cold hearth furnace melting uses the high-energy heating effect of the electron beam to melt and refine the ingot again, which can more thoroughly remove impurities and gases and improve the microstructure and performance of the ingot.
Preparation of tube billet
The ingot obtained by smelting is heated to an appropriate temperature, and then drilled to remove part of the metal in the center of the ingot to form a hollow tube billet. Then, the tube billet is placed in an extruder, and under the action of high temperature and high pressure, the tube billet is extruded into a tube of the required size and shape through a die. The drilling and extrusion process can produce tubes with uniform wall thickness and high dimensional accuracy.
Oblique rolling and piercing is to feed the heated ingot into the oblique rolling and piercing machine. Under the action of two inclined rollers and a head, the ingot is gradually pierced and rolled into a hollow tube billet. Oblique rolling and piercing has the advantages of high efficiency and low cost, and is suitable for manufacturing large quantities of titanium tubes with relatively fixed specifications.
Rolling is one of the important processes for titanium tube processing. Rolling the tube billet through a rolling mill can further reduce the wall thickness of the tube and improve the dimensional accuracy and surface quality of the tube. During the rolling process, cold rolling, hot rolling, multi-roll rolling, etc. are selected according to the specifications and performance requirements of the tube. Cold rolling can enable the tube to obtain higher dimensional accuracy and surface finish, and is suitable for high-precision, thin-walled titanium tubes. Hot rolling can improve the plasticity and toughness of the tube, and is suitable for large-diameter, thick-walled titanium tubes. Multi-roll rolling can accurately size and finish the tube, and improve the dimensional accuracy and roundness of the tube.
Drawing
Drawing is to pass the rolled tube through a drawing die, and reduce its diameter and thin its wall thickness under the action of tension, so as to obtain a tube of the desired size and shape. Drawing can further improve the strength and surface quality of the tube, and can also produce various special-shaped tubes. For example, titanium tubes with cross-sectional shapes such as square, oval, and triangle. During the drawing process, it is necessary to select appropriate drawing dies and lubricants to reduce the friction between the tube and the die.
Heat treatment
The purpose of annealing is to eliminate the internal stress of the tube, restore the plasticity and toughness of the tube, and improve the microstructure and performance of the tube. For titanium alloy tubes, in addition to annealing, solid solution treatment and aging treatment are also required to give full play to the role of alloy elements and improve the strength and hardness of the alloy. Aging treatment is to heat the titanium alloy tube after solid solution treatment to a lower temperature (generally between 480-560°C) and keep it warm for a certain period of time (ranging from several hours to tens of hours) to allow solute atoms to precipitate from the supersaturated solid solution to form a fine, dispersed strengthening phase, thereby improving the strength, hardness and wear resistance of the alloy.
Surface treatment
Pickling passivation is a common surface treatment method to remove scale, oil, impurities, etc. on the surface of titanium tubes, and to form a dense passivation film on the surface of the tube to improve its corrosion resistance. Mechanical polishing is to grind and polish the surface of titanium tubes using polishing wheels, sandpaper, etc. to reduce surface roughness and improve surface finish. Electrolytic polishing is suitable for application fields with extremely high requirements for surface quality, such as optical instruments, electronic devices, etc., and can meet the strict requirements of these fields for titanium tube surface accuracy and performance.
Quality inspection
Ultrasonic testing: Ultrasonic testing uses the phenomenon of reflection, refraction and scattering of ultrasonic waves when they propagate inside the titanium tube. By detecting the signal characteristics of the reflected wave, it is determined whether there are defects inside the tube, such as cracks, pores, inclusions, etc.
Chemical composition analysis: Chemical analysis is used to quantitatively analyze some elements that are difficult to accurately determine by spectral analysis, such as carbon, sulfur and other elements. Through strict chemical composition analysis, the quality of each batch of titanium tubes is guaranteed to be stable and the performance is reliable.
Mechanical properties test: The titanium tube is subjected to tensile test, hardness test, impact test and other mechanical properties tests to evaluate its strength, plasticity, toughness and other mechanical properties.
Metallurgical structure analysis: After cutting, grinding, polishing and corrosion of the tube sample using an optical microscope, electron microscope, etc., its metallographic structure characteristics are observed and compared with the standard metallographic map.
Wstitanium manufactures titanium tubes with a complex and sophisticated system that combines advanced technology, strict quality control and deep industry experience. From the careful selection and inspection of raw materials to smelting, ingot casting, tube blank preparation, tube machining, heat treatment, quality inspection and surface treatment, each link carries the pursuit of high-quality titanium tubes.